SirKen
New member
- 67
- 0
- 0
- Location
- Cocoa Florida
Starting with the area directly on top of the windshield frame. Needs to be flat-bar and needs to be able to cover the opening at the corners of the frame. Also want to be able to put a seal between the flat-bar and the windshield frame to keep some of the rain out. Measured the distance across and folded the flat-bar over at a 90 degree with a 1 inch overlap folded down.
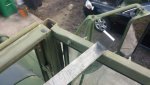
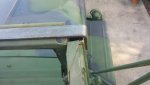
Next I removed the twist snaps from the soft top side frame (above the windows). I plan on using the frame from my soft top as part of my new hard top. The twist snaps simply unscrew making room for the flat-bar that will run to the back of the new hard top. This, again, will leave room for a seal to be installed between the soft top frame and the new hard top.
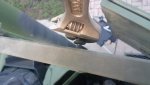
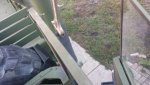
Next is to curve the flat-bar to conform with the curve of the rear of the cab. Made sure to measure from the front windshield frame to the rear of the cab since I plan on welding the side piece to the piece I just installed above the windshield frame. Made 2 of them and let them overlap at the rear of the cab with the intent to cut them and weld together into one piece.
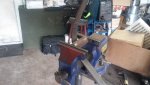
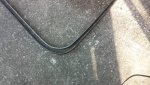
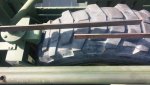
Cut them to fit and tapered the joint to get good penetration for the welder. Good thing I don't do this for a living... pretty it's not. Luckily, once I grind it smooth, no one will know.
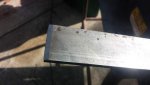

Next was to weld the "U" shaped flat-bar to the flat-bar that goes above the windshield. First I beveled the parts and made sure they lined up with each other... and were turned the correct way. Basically I ended up with a flat-bar band that will make up the perimeter of horizontal part of the hard top roof frame.
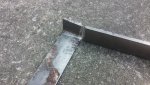
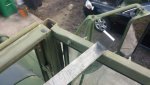
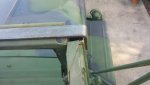
Next I removed the twist snaps from the soft top side frame (above the windows). I plan on using the frame from my soft top as part of my new hard top. The twist snaps simply unscrew making room for the flat-bar that will run to the back of the new hard top. This, again, will leave room for a seal to be installed between the soft top frame and the new hard top.
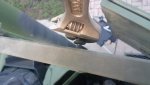
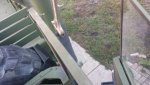
Next is to curve the flat-bar to conform with the curve of the rear of the cab. Made sure to measure from the front windshield frame to the rear of the cab since I plan on welding the side piece to the piece I just installed above the windshield frame. Made 2 of them and let them overlap at the rear of the cab with the intent to cut them and weld together into one piece.
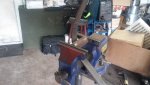
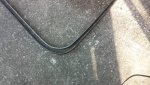
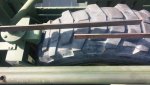
Cut them to fit and tapered the joint to get good penetration for the welder. Good thing I don't do this for a living... pretty it's not. Luckily, once I grind it smooth, no one will know.
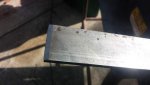

Next was to weld the "U" shaped flat-bar to the flat-bar that goes above the windshield. First I beveled the parts and made sure they lined up with each other... and were turned the correct way. Basically I ended up with a flat-bar band that will make up the perimeter of horizontal part of the hard top roof frame.
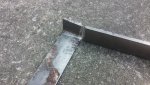