mesias
Member
- 62
- 55
- 18
- Location
- South Florida
Hey guys,
After all the help from this forum I managed to have this machine up and running. Without load it runs smoothly with almost no visible exhaust smoke. I have it now connected to the house electrical panel so all I needed was to complete a load test. For this I built a simple device, inspired by other members here, with a couple of 5400W dryer heat elements. This takes the genset to around 46 A or 85% of capacity.
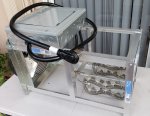
Before this test I've always found difficult to maintain the same frequency setting every time I start the genset. For some strange reason it'a always (with no load) above or below the 60HZ line. When I applied the load of a single heat element plus the fan, the genset took it with no trouble. Just a bit of smoke, the frequency went down a couple of lines but went right back up. This is how the gauges look with this load:
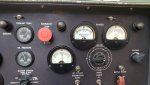
The first time I connected the second heater element... the gen set couldn't take it and it bogged down. I immediately removed the load and it recovered maintaining the previous load. I tried again a few times until the genset managed to take the additional load and hold the pace for it. I played for a while adding and removing the additional load and the genset would fail sometimes and other it would take the load. Every time it could assimilate the load the frequency dropped a few lines and you can hear the engine struggling.
In the process of "bogging down" this is what I observed:
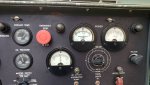
HERE is a video to the unit bogging down and HERE is another video of the unit running at 80% load. HERE is a video showing how the frequency drops and lags to recover after adding more load.
I'm suspecting this is related to the electrical fuel pump not copping with the demand. I read a post I needed to add a pressure gauge to test it but before spending more money in stuff I would like to hear your opinion. Here are some questions I have:
After all the help from this forum I managed to have this machine up and running. Without load it runs smoothly with almost no visible exhaust smoke. I have it now connected to the house electrical panel so all I needed was to complete a load test. For this I built a simple device, inspired by other members here, with a couple of 5400W dryer heat elements. This takes the genset to around 46 A or 85% of capacity.
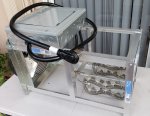
Before this test I've always found difficult to maintain the same frequency setting every time I start the genset. For some strange reason it'a always (with no load) above or below the 60HZ line. When I applied the load of a single heat element plus the fan, the genset took it with no trouble. Just a bit of smoke, the frequency went down a couple of lines but went right back up. This is how the gauges look with this load:
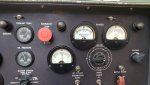
The first time I connected the second heater element... the gen set couldn't take it and it bogged down. I immediately removed the load and it recovered maintaining the previous load. I tried again a few times until the genset managed to take the additional load and hold the pace for it. I played for a while adding and removing the additional load and the genset would fail sometimes and other it would take the load. Every time it could assimilate the load the frequency dropped a few lines and you can hear the engine struggling.
In the process of "bogging down" this is what I observed:
- Heavy black smoke is thrown out (this could be from the wet stacking the unit has)
- The frequency dropped all the way down and you can hear the motor almost shutting down
- The coolant spilled from the relieve hose after overflowing the plastic container
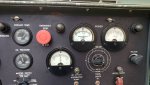
HERE is a video to the unit bogging down and HERE is another video of the unit running at 80% load. HERE is a video showing how the frequency drops and lags to recover after adding more load.
I'm suspecting this is related to the electrical fuel pump not copping with the demand. I read a post I needed to add a pressure gauge to test it but before spending more money in stuff I would like to hear your opinion. Here are some questions I have:
- Is the amount of back exhaust smoke "normal"?
- What could cause the motor to bog down like that?
- Why the coolant was spilled while losing power?
Attachments
-
159.6 KB Views: 56
Last edited: