- 1,836
- 987
- 113
- Location
- Paris KY
I am currently finishing up the front end of my P400 engine, checking the alternators and power steering alignment, and it occurred to me that it might be helpful for some of our junior members to understand why belts squeal and wear out quicker than they should. And then explain what to do to correct the adverse situation and eliminate the squealing, and lengthen belt life in the process.
Assuming belts are in good shape and are tensioned properly, they squeal and suffer premature wear/failure for one reason only - misalignment between 2 pulleys. The squeal happens when the misaligned and rotating belt contacts the inside edge of a pulley, and then must be twisted against that same side to run around the interior circumference of the pulley. This improper and constant contact produces heat and introduces stress to the filaments of the belt, similar to working a piece of wire back and forth between your hands to make the wire break.
To rectify the situation and permanently eliminate the squealing and extend belt life, here's what needs to be done -
First, temporarily remove your fan clutch assembly and re-install the 4 nuts back onto the studs of the water pump pulley; tighten securely, then use a straight edge ( I use my aluminum framing square ) to determine the alignment of the alternator pulleys with the straight edge. Because I am installing rebuilt Wilson 27Si alternators in original CUCV alternator brackets, for whatever reason my alternator pulleys were misaligned rearward just a smidgen more than 3/16". I reached out to Norm at KRC Power in Kennesaw Georgia and obtained a couple of .20 spacers to fit the .670 shaft of the alternators, and installed the spacers between the pulleys and the fans. This effectively moved both alternator pulleys forward precisely the correct amount for perfect alignment. Once I got the 2 alternators aligned with the water pump pulley, I then looked at the power steering pulley. It too was out of alignment rearward approximately the same amount. After thinking about this for a minute or so I figured the P400 timing gear cover, which is 34 years newer than the 6.2 OEM cover, was probably the reason the water pump pulley was positioned forward approximately .20". Interestingly, the CUCV crankshaft pulley, mounted onto the Fluidampr, which is mounted on the P400 crank snub, aligned perfectly with the water pump pulley. Back to the power steering pump pulley - It too needed to be moved forward approximately .20", so I grabbed my "pulley puller" (man that is a tounge twister) and pulled the power steering pulley forward until it aligned with the alternator pulley, water pump pulley, and crankshaft pulley. I checked/pulled/checked the alignement by sliding my straight edge down inside the alternator pulley and down inside the power steering pulley, until the straightedge aligned perfectly into the groove of the crankshaft pulley. Whew! That is a lot to say. Anyway, here are a few photos. There is no doubt in my mind that if you do this and install new Gates belts, your squealing will be over and your belts will last much longer. By the way, there are 2 bolts which must be loosened to adjust the passenger side alternator, 3 bolts for the drivers side alternator, and 4 bolts for the power steering pump. When tightening the belts, remember to tighten the power steering belt first, then the drivers side alternator, and lastly the passenger side alternator. Be careful in prying the power steering pump, as a screwdriver against the thin reservoir wall will puncture it. Lever the bracket, not the pump housing. After everything has been aligned and tightened, remove the 4 nuts from the studs in the water pump pulley and reinstal the fan clutch. Use blue Loktite on the threads.
Hope this helps.
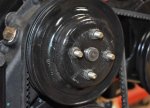
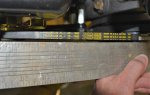
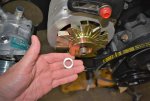
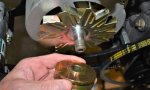
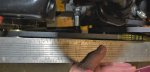
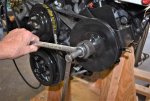
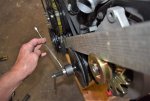
Assuming belts are in good shape and are tensioned properly, they squeal and suffer premature wear/failure for one reason only - misalignment between 2 pulleys. The squeal happens when the misaligned and rotating belt contacts the inside edge of a pulley, and then must be twisted against that same side to run around the interior circumference of the pulley. This improper and constant contact produces heat and introduces stress to the filaments of the belt, similar to working a piece of wire back and forth between your hands to make the wire break.
To rectify the situation and permanently eliminate the squealing and extend belt life, here's what needs to be done -
First, temporarily remove your fan clutch assembly and re-install the 4 nuts back onto the studs of the water pump pulley; tighten securely, then use a straight edge ( I use my aluminum framing square ) to determine the alignment of the alternator pulleys with the straight edge. Because I am installing rebuilt Wilson 27Si alternators in original CUCV alternator brackets, for whatever reason my alternator pulleys were misaligned rearward just a smidgen more than 3/16". I reached out to Norm at KRC Power in Kennesaw Georgia and obtained a couple of .20 spacers to fit the .670 shaft of the alternators, and installed the spacers between the pulleys and the fans. This effectively moved both alternator pulleys forward precisely the correct amount for perfect alignment. Once I got the 2 alternators aligned with the water pump pulley, I then looked at the power steering pulley. It too was out of alignment rearward approximately the same amount. After thinking about this for a minute or so I figured the P400 timing gear cover, which is 34 years newer than the 6.2 OEM cover, was probably the reason the water pump pulley was positioned forward approximately .20". Interestingly, the CUCV crankshaft pulley, mounted onto the Fluidampr, which is mounted on the P400 crank snub, aligned perfectly with the water pump pulley. Back to the power steering pump pulley - It too needed to be moved forward approximately .20", so I grabbed my "pulley puller" (man that is a tounge twister) and pulled the power steering pulley forward until it aligned with the alternator pulley, water pump pulley, and crankshaft pulley. I checked/pulled/checked the alignement by sliding my straight edge down inside the alternator pulley and down inside the power steering pulley, until the straightedge aligned perfectly into the groove of the crankshaft pulley. Whew! That is a lot to say. Anyway, here are a few photos. There is no doubt in my mind that if you do this and install new Gates belts, your squealing will be over and your belts will last much longer. By the way, there are 2 bolts which must be loosened to adjust the passenger side alternator, 3 bolts for the drivers side alternator, and 4 bolts for the power steering pump. When tightening the belts, remember to tighten the power steering belt first, then the drivers side alternator, and lastly the passenger side alternator. Be careful in prying the power steering pump, as a screwdriver against the thin reservoir wall will puncture it. Lever the bracket, not the pump housing. After everything has been aligned and tightened, remove the 4 nuts from the studs in the water pump pulley and reinstal the fan clutch. Use blue Loktite on the threads.
Hope this helps.
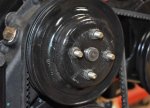
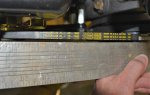
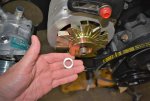
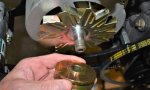
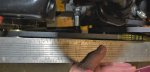
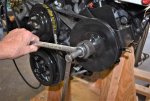
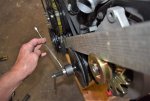
Last edited: