Freedom Land Clearing
Member
- 32
- 26
- 18
- Location
- Montoursville, PA
Good morning,
I have a 1998 M1088A0 with a CTIS issue—go figure. The ECU is flashing 5 lights.
This site has assisted a bit in initial troubleshooting by providing the Dana troubleshooting guide as well as the TMs.
Doing the first couple of steps in the TM lead me to an electrical issue. Why? There are no bursts of air at port C on the manifold.
One thing I want to put out there is this: someone has been in the ECU plug/harness before me. What I found were two wires twisted together just behind the plug. That wire appears to be connected to pin Z. See pics. Looking at the face of the plug, there are only 15 pins in the pin slots…leaving a handful empty. Looking at the harness going into the back of the plug, there are only 14 wires. I stripped like 6” of insulation hoping to find a snipped wire and see no evidence of a 15th wire. So, there is one snipped wire on the back of the plug doing nothing.
Ideas?
Thanks.
John
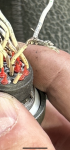
I have a 1998 M1088A0 with a CTIS issue—go figure. The ECU is flashing 5 lights.
This site has assisted a bit in initial troubleshooting by providing the Dana troubleshooting guide as well as the TMs.
Doing the first couple of steps in the TM lead me to an electrical issue. Why? There are no bursts of air at port C on the manifold.
One thing I want to put out there is this: someone has been in the ECU plug/harness before me. What I found were two wires twisted together just behind the plug. That wire appears to be connected to pin Z. See pics. Looking at the face of the plug, there are only 15 pins in the pin slots…leaving a handful empty. Looking at the harness going into the back of the plug, there are only 14 wires. I stripped like 6” of insulation hoping to find a snipped wire and see no evidence of a 15th wire. So, there is one snipped wire on the back of the plug doing nothing.
Ideas?
Thanks.
John
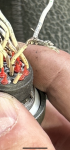
Last edited: