Rebar
Member
- 52
- 0
- 6
- Location
- St. Louis/Missouri
The winch cable was pulled out of the chain connector lock nut on GL acquired M817. Finally got the locknut loose. What are the secrets to getting a secure connection? Do I pass the lock nut up on the cable end, 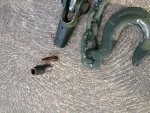
put the anvil in the base and then just tighten it down? How far do you push the cable through to get it locked by the anvil and nut assembly? I have never done this before and cannot find a page describing procedure in TM. Obviously this is critical step if I ever want to have a functioning winch on M817. Any tips would be appreciated.
Rebar
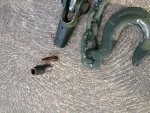
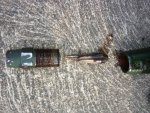
Rebar