ATPTac
Member
- 379
- 5
- 16
- Location
- Charlotte, North Carolina
Well I was initially going to wait until I got the rear axles done and do one big write up, but its looking like its going to be a while before I'm going to be able to get to the rears. So I'm going to go ahead and do my write up for the fronts and do the rears later. I know this has been done on here before, but I figured a fresh thread with a different perspective couldn't hurt.
All in all it wasn't a bad job, a little time consuming (had a few mishaps which I'll get to later), and extremely messy. I'm going to do this write up as if it were intended for someone who has never turned a wrench before as best I can, so for the "veterans" on here this going to seem a little excessively dumbed down. Now on to the write up:
First things first, the front wheels have to be removed. Obviously you need to jack up the front axle before doing so (and don't forget to break the lugs loose before hand). For those that don't know, the drivers side of the truck are left hand thread (left tight, right loose) assuming nobody previously replaced them with right hand thread. The end of the studs should be stamped with either a "R" or "L" indicating which thread direction they are. The general rule of thumb is if you're starting a breaker bar at the 12 o'clock position on the lug nut you always turn to the rear of the truck to loosen. To jack up the truck you can pick up a 6+ ton bottle jack or use an applicable floor jack and then ALWAYS put jack stands under the axle and lower onto them before proceeding (I got 12 ton jack stands from Harbor Freight).
Now back onto getting the lug nuts loose. There are several different ways to get lugs loose: torque multipliers, 3/4" and up impact guns, breaker bars, etc... I ended up buying a combo 1 1/2" and Budd socket from snap on to use and just put it on a 3/4" breaker bar and went to Lowe's and bought a 6' pipe to put on the breaker bar to bust the nuts loose. It took a little bit of muscle, but they cracked loose relatively easy. There are tons of threads on the subject, and everyone has their own way of doing it. I needed the socket regardless, and the pipe only cost me $18, plus the 3/4" breaker bar.
Now that the wheel is off, the drum assembly is exposed and the fun begins!
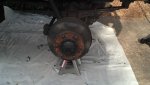
The next step is the remove the 8 bolts that hold the hub on. Frankly, I didn't think this through and did it after the wheel was off. So I put my ratchet on and hit it a couple times to loosen the bolts, vs. if you do it with the tire on the ground you won't need to hurt your hand or ding up your ratchet with a hammer. Not really a huge deal, but it would be easier to do before removing the tire.
Once you get the hub off you'll be able to see the 3" 8 point nuts and lock washer between them. Use a 3" 8 point socket to remove the outer nut:
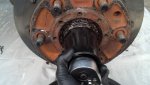
After you get the outer nut off, use a chisel and tap the ears on the lock washer back flush so you can easily remove it. It just slides off, you might need to lightly pry on it a little bit. Once off you'll just have the inner nut and bearing left:
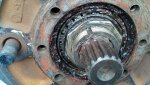
Once again use the 3" socket to remove the inner nut. Then its just the outer wheel bearing left holding the drum on:
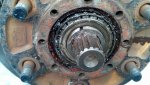
If you give the drum a little wiggle and tug, it should pop the bearing loose. Remove the bearing and set it aside for packing later:
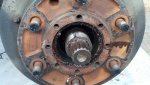
Once the bearing is removed you can remove the drum. The drums are deceptively heavy, so either get someone to help you with it or make sure you have some decent upper body strength and a good grip on the drum so you can gently pull it off and set it aside. Once that's removed you now have access to the brake shoes and wheel cylinder:
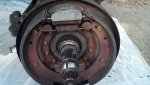
As you can see the wheel cylinder (top middle) has a cover over it. This is where I started to brain fart and forgot to take some pictures. But if you look on the back of the brake assembly there are 2 bolts that old the wheel cylinder in, as well as the brake hose. Take the hose loose, and the 2 bolts that hold the wheel cylinder in. The shield is held in between the cylinder and the backing plate and will come loose once the 2 bolts are removed. Then you can take the wheel cylinder and shield out (this can also be done after removing the backing plate minus the hose, which is actually easier to do it that way):
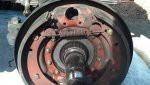
Next you need to remove the 12 nuts that hold the backing plate on. As you can see in the following picture a pretty good chunk of mine pulled the studs out with the nuts (don't lose the small lock washers behind the nuts). There is a ring that's under the nuts that comes off first then the spindle, then the backing plate. After that comes off you can pull your axle assembly out: (sorry for the lack of pictures in these steps, it was rather greasy and I couldn't get my phone out without ruining it)
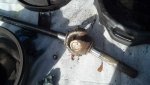
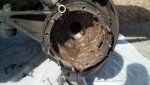
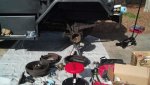
All in all it wasn't a bad job, a little time consuming (had a few mishaps which I'll get to later), and extremely messy. I'm going to do this write up as if it were intended for someone who has never turned a wrench before as best I can, so for the "veterans" on here this going to seem a little excessively dumbed down. Now on to the write up:
First things first, the front wheels have to be removed. Obviously you need to jack up the front axle before doing so (and don't forget to break the lugs loose before hand). For those that don't know, the drivers side of the truck are left hand thread (left tight, right loose) assuming nobody previously replaced them with right hand thread. The end of the studs should be stamped with either a "R" or "L" indicating which thread direction they are. The general rule of thumb is if you're starting a breaker bar at the 12 o'clock position on the lug nut you always turn to the rear of the truck to loosen. To jack up the truck you can pick up a 6+ ton bottle jack or use an applicable floor jack and then ALWAYS put jack stands under the axle and lower onto them before proceeding (I got 12 ton jack stands from Harbor Freight).
Now back onto getting the lug nuts loose. There are several different ways to get lugs loose: torque multipliers, 3/4" and up impact guns, breaker bars, etc... I ended up buying a combo 1 1/2" and Budd socket from snap on to use and just put it on a 3/4" breaker bar and went to Lowe's and bought a 6' pipe to put on the breaker bar to bust the nuts loose. It took a little bit of muscle, but they cracked loose relatively easy. There are tons of threads on the subject, and everyone has their own way of doing it. I needed the socket regardless, and the pipe only cost me $18, plus the 3/4" breaker bar.
Now that the wheel is off, the drum assembly is exposed and the fun begins!
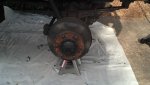
The next step is the remove the 8 bolts that hold the hub on. Frankly, I didn't think this through and did it after the wheel was off. So I put my ratchet on and hit it a couple times to loosen the bolts, vs. if you do it with the tire on the ground you won't need to hurt your hand or ding up your ratchet with a hammer. Not really a huge deal, but it would be easier to do before removing the tire.
Once you get the hub off you'll be able to see the 3" 8 point nuts and lock washer between them. Use a 3" 8 point socket to remove the outer nut:
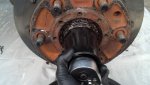
After you get the outer nut off, use a chisel and tap the ears on the lock washer back flush so you can easily remove it. It just slides off, you might need to lightly pry on it a little bit. Once off you'll just have the inner nut and bearing left:
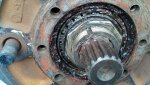
Once again use the 3" socket to remove the inner nut. Then its just the outer wheel bearing left holding the drum on:
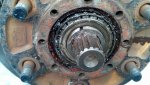
If you give the drum a little wiggle and tug, it should pop the bearing loose. Remove the bearing and set it aside for packing later:
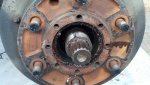
Once the bearing is removed you can remove the drum. The drums are deceptively heavy, so either get someone to help you with it or make sure you have some decent upper body strength and a good grip on the drum so you can gently pull it off and set it aside. Once that's removed you now have access to the brake shoes and wheel cylinder:
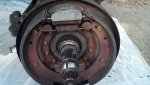
As you can see the wheel cylinder (top middle) has a cover over it. This is where I started to brain fart and forgot to take some pictures. But if you look on the back of the brake assembly there are 2 bolts that old the wheel cylinder in, as well as the brake hose. Take the hose loose, and the 2 bolts that hold the wheel cylinder in. The shield is held in between the cylinder and the backing plate and will come loose once the 2 bolts are removed. Then you can take the wheel cylinder and shield out (this can also be done after removing the backing plate minus the hose, which is actually easier to do it that way):
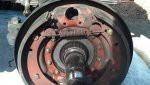
Next you need to remove the 12 nuts that hold the backing plate on. As you can see in the following picture a pretty good chunk of mine pulled the studs out with the nuts (don't lose the small lock washers behind the nuts). There is a ring that's under the nuts that comes off first then the spindle, then the backing plate. After that comes off you can pull your axle assembly out: (sorry for the lack of pictures in these steps, it was rather greasy and I couldn't get my phone out without ruining it)
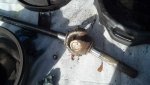
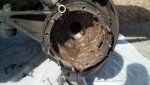
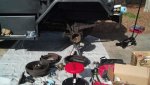