rustystud
Well-known member
- 9,400
- 3,376
- 113
- Location
- Woodinville, Washington
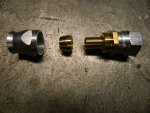
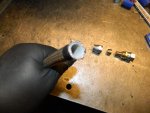
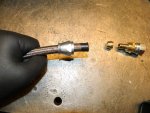
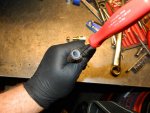
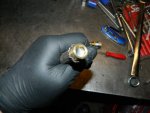
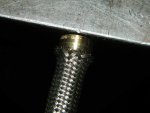
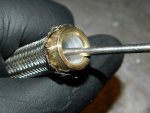
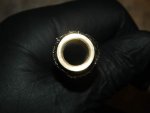
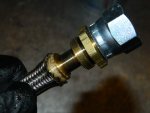
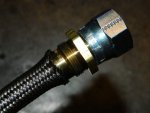
Last edited:
Steel Soldiers now has a few new forums, read more about it at: New Munitions Forums!
Yes, if you don't get a good straight cut on the hose sometimes you need to use a knife to clean it up. On the aluminum fittings I use anti-sieze, but I'm sure motor oil will work OK .1 thing I can add is that after cutting the line, I suggest deburring the edge of the teflon with a razor knife. It allows the Ferrule (olive) to seat better on the end of the line.
They also make aluminum hose ends. If using these I recommend motor oil on the threads to prevent galling.
Good looking engine you have there Neophyte .Awesome write up!! I used a the same hose for fuel lines on a DD453 I rebuilt over the winter. The critical part was cutting the braided hose with a fiber cut off wheel (took a couple tries to figure out that was the best method). Once the braid comes undone.....impossible to connect the compression fitting on.
View attachment 514280
They are the "cats meow ! " I see you used the aluminum fittings. I always just use the steel ones, that way I can recycle them to use on hydraulic systems if I need to.Thank you. I wish this write up was available 6 months ago.......I must of cut the braided hose 4 times before getting it right. I used 8an fittings throughout the fuel system...worked like a charm. These PTFE hoses are a huge step up from the old rubber hoses.
We get it, advertisements are annoying!
Sure, ad-blocking software does a great job at blocking ads, but it also blocks useful features of our website like our supporting vendors. Their ads help keep Steel Soldiers going. Please consider disabling your ad blockers for the site. Thanks!