1stDeuce
Member
- 351
- 18
- 18
- Location
- Mancos, CO
Greetings! I'm going to use these trailers as a base for brush fire units, and using a 12" riser for the hitch just isn't a great option.
Of course the first thing I did was to pull the runflat 37's and toss on some 285's. That brought the hitch down 2" or so, but it's still too high. In scoping out the axle mounting, I decided it wouldn't be that hard to do some cutting and push the axle up under the trailer a bit. As they are, the axle mounting pad is almost exactly 5" below the frame tube. If you put it all the way up against the bottom of the frame, you could drop the trailer 5". the downside to that is that you'd only be able to use the side bolts, which might be fine, but I didn't want to go that route.
Here's what I started with...
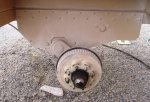
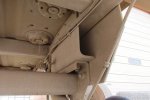
I ended up buying some 2-1/2" square 1/4" wall aluminum tube. I cut the pieces to ~14" long to put between the axle and frame so I could bolt the axle to the square tube, and then bolt the square tube to what was left of the inside plate after I cut ~2-1/2" off of it. I moved the outer plate holes up 2-1/2" and re-trimmed it, like I have scribed below:
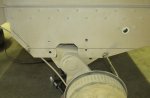
On the inside, I had to drill out the rivets holding the brake line to the inner plate before I could cut it off. Actually had to drill out the forward one too, though I hadn't figured that out yet when I took this picture. It was easier to just grind the head off and punch it through. They're tough!!
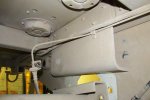
I chopped the inner and outer plates 2-1/2" with my plasma cutter, and then made the notch for the axle to fit in. It turns out the side plate material is pretty soft. The 6061 T6 square tube that I bought was noticeably harder. I think you could pretty easily saw the same lines with a sawzall or jigsaw and a coarse metal blade.
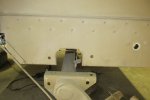
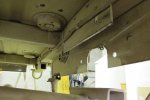
Once I got this far, I put the square tube (With holes drilled for the axle bolts) between the two pieces and jacked the axle into place. Here it is with all the bolts loosely installed.
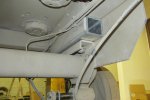
I jacked it up by the axle to seat it against the bottom of the trailer. Made measurements to ensure the axle was relatively square and shifted it around some before tightening all four bolts.
<Edit - 1/28/15> Here are some pictures of the finished product all bolted and riveted and done aside from paint. This is actually the second trailer that I did, and I moved the axle forward 1/2", which seems to work out well. (But I forgot to drill the holes in my square tube 1/2" forward, so it's not centered in the old bracket... Oops.)
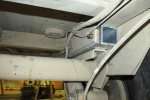
Here's a side shot showing the shock travel left. This will be fine.
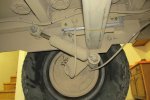
And finally, the tire is still pretty centered in the wheel well. Actually, it's just slightly forward of center, but on the first trailer I did, it seemed to end up just back from center. I'm moving them all at least 1/2" forward from now on! (This is only a 265 tire because that's what came on the rim.)
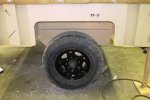
I did note that the first trailer, the shocks only have about 3" of total travel, even though they look like they would have much more... In stock configuration, they were fully extended with the tire off the ground, and though they look like they can compress about 4", the last inch of travel doesn't seem to be available. ??
Here's a final pic. The lunette is now right at 24" with the trailer empty and level. I can work with that!! The tires fit the wheel openings pretty well too! There's 7-1/2" between the top of the tire and the bottom side of the wheel well, so I'm pretty sure it would be OK lowered a full 5". I'll probably do the other two trailers like this though, since I have enough square tube for both. I think 24" hitch height will be OK for most pickups with a slight raised mount, or some lift on the truck.
Chris
Of course the first thing I did was to pull the runflat 37's and toss on some 285's. That brought the hitch down 2" or so, but it's still too high. In scoping out the axle mounting, I decided it wouldn't be that hard to do some cutting and push the axle up under the trailer a bit. As they are, the axle mounting pad is almost exactly 5" below the frame tube. If you put it all the way up against the bottom of the frame, you could drop the trailer 5". the downside to that is that you'd only be able to use the side bolts, which might be fine, but I didn't want to go that route.
Here's what I started with...
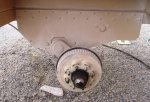
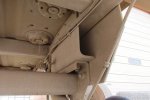
I ended up buying some 2-1/2" square 1/4" wall aluminum tube. I cut the pieces to ~14" long to put between the axle and frame so I could bolt the axle to the square tube, and then bolt the square tube to what was left of the inside plate after I cut ~2-1/2" off of it. I moved the outer plate holes up 2-1/2" and re-trimmed it, like I have scribed below:
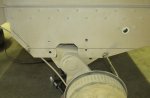
On the inside, I had to drill out the rivets holding the brake line to the inner plate before I could cut it off. Actually had to drill out the forward one too, though I hadn't figured that out yet when I took this picture. It was easier to just grind the head off and punch it through. They're tough!!
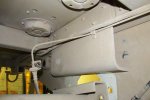
I chopped the inner and outer plates 2-1/2" with my plasma cutter, and then made the notch for the axle to fit in. It turns out the side plate material is pretty soft. The 6061 T6 square tube that I bought was noticeably harder. I think you could pretty easily saw the same lines with a sawzall or jigsaw and a coarse metal blade.
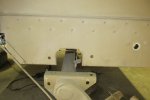
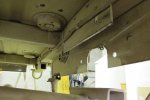
Once I got this far, I put the square tube (With holes drilled for the axle bolts) between the two pieces and jacked the axle into place. Here it is with all the bolts loosely installed.
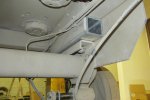
I jacked it up by the axle to seat it against the bottom of the trailer. Made measurements to ensure the axle was relatively square and shifted it around some before tightening all four bolts.
<Edit - 1/28/15> Here are some pictures of the finished product all bolted and riveted and done aside from paint. This is actually the second trailer that I did, and I moved the axle forward 1/2", which seems to work out well. (But I forgot to drill the holes in my square tube 1/2" forward, so it's not centered in the old bracket... Oops.)
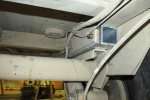
Here's a side shot showing the shock travel left. This will be fine.
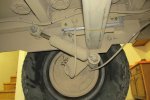
And finally, the tire is still pretty centered in the wheel well. Actually, it's just slightly forward of center, but on the first trailer I did, it seemed to end up just back from center. I'm moving them all at least 1/2" forward from now on! (This is only a 265 tire because that's what came on the rim.)
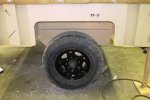
I did note that the first trailer, the shocks only have about 3" of total travel, even though they look like they would have much more... In stock configuration, they were fully extended with the tire off the ground, and though they look like they can compress about 4", the last inch of travel doesn't seem to be available. ??
Here's a final pic. The lunette is now right at 24" with the trailer empty and level. I can work with that!! The tires fit the wheel openings pretty well too! There's 7-1/2" between the top of the tire and the bottom side of the wheel well, so I'm pretty sure it would be OK lowered a full 5". I'll probably do the other two trailers like this though, since I have enough square tube for both. I think 24" hitch height will be OK for most pickups with a slight raised mount, or some lift on the truck.
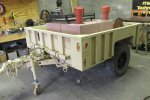
Chris
Last edited: