- 204
- 9
- 18
- Location
- Odessa, Florida
As much as I love the feel of a good workout, and don't mind herniating myself on the regular, I started looking for ways to help ease the pain of lifting the tailgate. It was actually a combo of that, and forgetting to latch and having the thing slam down in traffic (when you look back and think hmmm... did i just back over a Honda?).
The Deuce forum had some great ideas about 4 years ago, none of which seemed to materialize. There's talk of cables and garage door springs... But the price of the ramp hinge is almost negligible. So, two 5/8" rods, two 3/4" spring hinges (LH and RH), and a little light metal cutting/grinding...
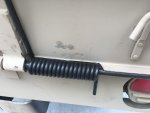
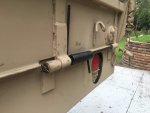
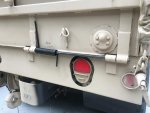
I was thinking of welding the top bar of the spring... But I like the removability. I've ZERO welding experience. But I'm thinking of starting. I'm working with a lot of metal lately, and there's a hundred different projects that I say to myself, "I wish I could get someone over here to do a weld"... That's a different topic though.
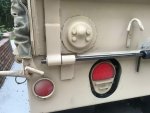
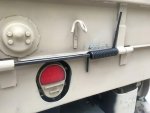
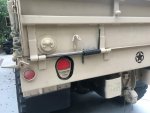
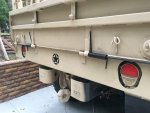
https://youtu.be/QtqLy-DXiDs
The Deuce forum had some great ideas about 4 years ago, none of which seemed to materialize. There's talk of cables and garage door springs... But the price of the ramp hinge is almost negligible. So, two 5/8" rods, two 3/4" spring hinges (LH and RH), and a little light metal cutting/grinding...
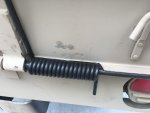
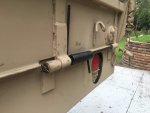
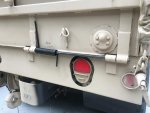
I was thinking of welding the top bar of the spring... But I like the removability. I've ZERO welding experience. But I'm thinking of starting. I'm working with a lot of metal lately, and there's a hundred different projects that I say to myself, "I wish I could get someone over here to do a weld"... That's a different topic though.
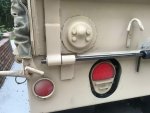
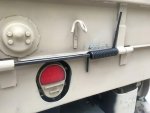
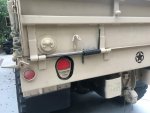
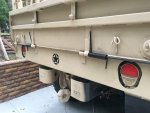
https://youtu.be/QtqLy-DXiDs
Last edited: