Kenny0
Active member
- 121
- 30
- 28
- Location
- Leland, Iowa
I have a MEP 802, so I will be using the MEP 802 specifications for the meter calibrations.
I have mine set up for single phase 240 V.
That would be 26 At 240 V or 52 A at 120 V
This process will work on most other generators. Just use the specifications for your generator.
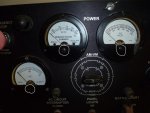
I will start with the voltage meter, I usually leave this to monitor 240 V. first off you need an accurate meter to measure with. Attach your meter to the output lugs with the engine off. Then start the engine and adjust the voltage to 240 V with the meter you just attached. If the panel meter does not read the correct voltage use a screwdriver and turn the adjustment screw on the gauge, this is located just below the glass on the gauge. Use the biggest screwdriver that will go in that slot. Shut off the engine and disconnect your meter, you are done.
Next we'll go with the frequency meter. I think the best way is to use a kill a Watt meter or a multimeter with a frequency setting. My kill a Watt meter when plugged into a utility line reads between 59.9 and 60 Hz, so we should be good. Connect your frequency meter to the convenience outlet either directly or through an extension cord. Start the generator and let it run long enough to stabilize everything. Adjust the frequency control on the generator for 60 Hz with your meter then check your panel meter and if it does not read the same make the same adjustment as above, to · 60 Hz, you are done.
There is another way to check your frequency, and that is with a tachometer.1800 RPM will give you exactly 60 Hz. If you have a 2 pole generator, 3600 RPM would be exactly 60 Hz. I think the best tachometer would be an optical tachometer, that would be one where you would place a reflective tape on whatever you are measuring the RPM, the second choice would be a mechanical tachometer, this would not be as accurate, and would be the most dangerous because you would have your fingers hand and arm in the direct vicinity of rotating parts. Another option would be a diesel timing light, that has a transducer that is clamped on the line of injector number one, this would also measure your RPM accurately. On a gasoline engine there is also another option, a tachometer with an antenna which is held close to your spark plugs. These can be a little finicky. With this you would have to know if there is a waste spark, if you have one of these you would probably know what I mean.
Next up is the battery charge meter. This will be checked with the engine stopped. With the engine stopped the gauge should be right on zero. If not, adjust the screw as mentioned above. Any time you make an adjustment, tap the gauge with your finger and make sure it still reads zero. When you read zero you're done.
The last gauge calibration will be the current meter. Some people call this the load meter or a power meter. Remember, this meter is only used for generator output. First we need at 26 amp load for 240 V, it can be a combination of inductive and resistive load. The resistive load should be half or more of the total load, this will become clear later. Also 2 incandescent lightbulbs hooked up in series can be used to fine-tune the load. 2 300w bulbs would be 600W total. Next, we need an accurate amp meter to monitor one leg of the 220 V. A clamp on amp meter would be the easiest as long as it is accurate. Start the generator let it warm up and apply the load. Fine-tune the load to get as close to 26 A as possible, if you are within one amp or so use a voltage adjustment to fine-tune to 26 A. Let the generator stabilize at that load and look and see if your amp meter is still reading 26 A, if not fine-tune with the voltage control. The load meter on the panel should be reading 100%, if not the just as above. You are done.
Remember, this gauge reads the output load of the generator only. There can be a big difference between power produced and power used. I have another post that I think would explain that - https://www.steelsoldiers.com/showthread.php?171845-My-Generator-Won-t-Run-a-2825-Watt-Load
This post was longer than I wanted it to be, but I am a detail person. That is one of the traits of being in Aspie.
I have mine set up for single phase 240 V.
That would be 26 At 240 V or 52 A at 120 V
This process will work on most other generators. Just use the specifications for your generator.
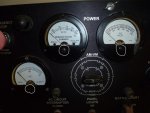
I will start with the voltage meter, I usually leave this to monitor 240 V. first off you need an accurate meter to measure with. Attach your meter to the output lugs with the engine off. Then start the engine and adjust the voltage to 240 V with the meter you just attached. If the panel meter does not read the correct voltage use a screwdriver and turn the adjustment screw on the gauge, this is located just below the glass on the gauge. Use the biggest screwdriver that will go in that slot. Shut off the engine and disconnect your meter, you are done.
Next we'll go with the frequency meter. I think the best way is to use a kill a Watt meter or a multimeter with a frequency setting. My kill a Watt meter when plugged into a utility line reads between 59.9 and 60 Hz, so we should be good. Connect your frequency meter to the convenience outlet either directly or through an extension cord. Start the generator and let it run long enough to stabilize everything. Adjust the frequency control on the generator for 60 Hz with your meter then check your panel meter and if it does not read the same make the same adjustment as above, to · 60 Hz, you are done.
There is another way to check your frequency, and that is with a tachometer.1800 RPM will give you exactly 60 Hz. If you have a 2 pole generator, 3600 RPM would be exactly 60 Hz. I think the best tachometer would be an optical tachometer, that would be one where you would place a reflective tape on whatever you are measuring the RPM, the second choice would be a mechanical tachometer, this would not be as accurate, and would be the most dangerous because you would have your fingers hand and arm in the direct vicinity of rotating parts. Another option would be a diesel timing light, that has a transducer that is clamped on the line of injector number one, this would also measure your RPM accurately. On a gasoline engine there is also another option, a tachometer with an antenna which is held close to your spark plugs. These can be a little finicky. With this you would have to know if there is a waste spark, if you have one of these you would probably know what I mean.
Next up is the battery charge meter. This will be checked with the engine stopped. With the engine stopped the gauge should be right on zero. If not, adjust the screw as mentioned above. Any time you make an adjustment, tap the gauge with your finger and make sure it still reads zero. When you read zero you're done.
The last gauge calibration will be the current meter. Some people call this the load meter or a power meter. Remember, this meter is only used for generator output. First we need at 26 amp load for 240 V, it can be a combination of inductive and resistive load. The resistive load should be half or more of the total load, this will become clear later. Also 2 incandescent lightbulbs hooked up in series can be used to fine-tune the load. 2 300w bulbs would be 600W total. Next, we need an accurate amp meter to monitor one leg of the 220 V. A clamp on amp meter would be the easiest as long as it is accurate. Start the generator let it warm up and apply the load. Fine-tune the load to get as close to 26 A as possible, if you are within one amp or so use a voltage adjustment to fine-tune to 26 A. Let the generator stabilize at that load and look and see if your amp meter is still reading 26 A, if not fine-tune with the voltage control. The load meter on the panel should be reading 100%, if not the just as above. You are done.
Remember, this gauge reads the output load of the generator only. There can be a big difference between power produced and power used. I have another post that I think would explain that - https://www.steelsoldiers.com/showthread.php?171845-My-Generator-Won-t-Run-a-2825-Watt-Load
This post was longer than I wanted it to be, but I am a detail person. That is one of the traits of being in Aspie.
Last edited: