- 1,128
- 2,143
- 113
- Location
- Wauchula, FL
I'm wanting to have a single place to get all the information for everything involved with changing the 12/24 volt alternator with a readily available 24 volt alternator and 24 to 12 volt equalizer.
I'm Primarily speaking about an A1 truck.
First the Title of this thread. While doing days of research I've come across many threads relating to this but the title never led me there easily. If you have a good suggestion on a better title please share it and i can change it.
Second I want to start with keeping the change as simple as possible but maintain all the functions, such as the charging system indicator light. Later maybe add different more complicated ways of doing it.
Third explaining what each device is, what it does and why. If you must use abbreviations preface it with the full words and include pictures and diagrams or hand drawings. So anyone can understand what you are referring to.
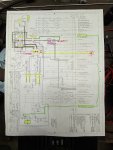
Using this image for primary reference we can identify most of the components we will be discussing.
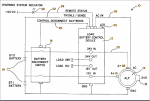
Load Battery Control/Charge Device "LBCD"
Found the Patent for this with a reasonable description.
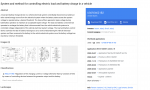
I'll start by asking a few general questions that I have so we further understand why we are doing this.
1: Is the original alternator really bad or is the miss use of the vehicle the cause of the alternator failure? Such as letting it sit for long periods of time and depleting the batteries more the reason?
2: Load Battery Control Device "LBCD" why is it there, why should we get rid of it? Because it's a stupid design? Because it Failed? Because???
I have plenty more questions but I want to try keeping it easy to follow.
I'm Primarily speaking about an A1 truck.
First the Title of this thread. While doing days of research I've come across many threads relating to this but the title never led me there easily. If you have a good suggestion on a better title please share it and i can change it.
Second I want to start with keeping the change as simple as possible but maintain all the functions, such as the charging system indicator light. Later maybe add different more complicated ways of doing it.
Third explaining what each device is, what it does and why. If you must use abbreviations preface it with the full words and include pictures and diagrams or hand drawings. So anyone can understand what you are referring to.
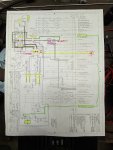
Using this image for primary reference we can identify most of the components we will be discussing.
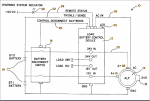
Load Battery Control/Charge Device "LBCD"
Found the Patent for this with a reasonable description.
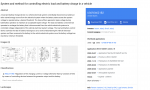
I'll start by asking a few general questions that I have so we further understand why we are doing this.
1: Is the original alternator really bad or is the miss use of the vehicle the cause of the alternator failure? Such as letting it sit for long periods of time and depleting the batteries more the reason?
2: Load Battery Control Device "LBCD" why is it there, why should we get rid of it? Because it's a stupid design? Because it Failed? Because???
I have plenty more questions but I want to try keeping it easy to follow.