Ronmar
Well-known member
- 4,322
- 8,167
- 113
- Location
- Port angeles wa
4 anchor pockets(3x5”?) welded to the upper 6” frame channel near front and rear. The rear crane lift point is also incorporated into that upper channel just forward of the rear wheel. The box is attached to a box tube subframe that has 4 feet that rest in the pockets on 1/2” rubber pads. There is a large bolt hole down thru the middle of each foot/pocket. Two have nuts and bolts, the other two have long bolts with captive springs. I looked up what I thought was the spring specs once upon a time. If I recall correctly, they have a little over 2” of total compression @ ~1000#/in rate…Interesting thread read. Out of curiosity, how is the factory M1079 Van body attached?
i bought a M1079 cab and chassis at auction. You can see the remnants of my pockets(cut the walls of the pockets off flush with the top of the frame) in this pic…
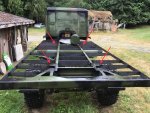
Last edited: