After starting reassembling and starting this unit up, I through a load on it. The unit was very shaky for a 802a, even after I tighten some loose isolator bolts. The unit could pull 6000 watts and seemed to be running fine, but anything over 3000 watts and the overload fault would trip after a minute or so. On the suggestion of a few members, I bought some Deoxit and hosed the S6 and S8 and exercised them thoroughly. I haven't retested it yet because the vibration issue really needs to be addressed. I fired up my other 802a for comparison and this one is much worse, so something is going on.
Since this unit had major oil pressure issues due to a stuck relief valve, I pulled the valve covers and inspected the push rods for bending per the TM. All looked good, so I reassembled the unit per the book procedure, waiting 90 minutes before hand turning the engine and restarting it. I also pulled the back cover of the genhead and look for a loose bearing. All looked good there. I also made sure the IPs were rotated to the same position, fully counterclockwise. It's worth mentioning that it seems to run good, pulls a full load, and the exhaust manifold is nice and dry with minimum soot buildup.
The front of the engine / genhead combo moves considerably more on its isolators then the rear. I've been thinking about what Guyfang has mentioned in several threads about the isolators, especially since the forward ones were missing hardware like someone had been messing with them. I'll look for part numbers tomorrow when the light is better, but here is some slow motion video of both. It doesn't look good.
www.youtube.com
www.youtube.com
What do you all think?
Since this unit had major oil pressure issues due to a stuck relief valve, I pulled the valve covers and inspected the push rods for bending per the TM. All looked good, so I reassembled the unit per the book procedure, waiting 90 minutes before hand turning the engine and restarting it. I also pulled the back cover of the genhead and look for a loose bearing. All looked good there. I also made sure the IPs were rotated to the same position, fully counterclockwise. It's worth mentioning that it seems to run good, pulls a full load, and the exhaust manifold is nice and dry with minimum soot buildup.
The front of the engine / genhead combo moves considerably more on its isolators then the rear. I've been thinking about what Guyfang has mentioned in several threads about the isolators, especially since the forward ones were missing hardware like someone had been messing with them. I'll look for part numbers tomorrow when the light is better, but here is some slow motion video of both. It doesn't look good.
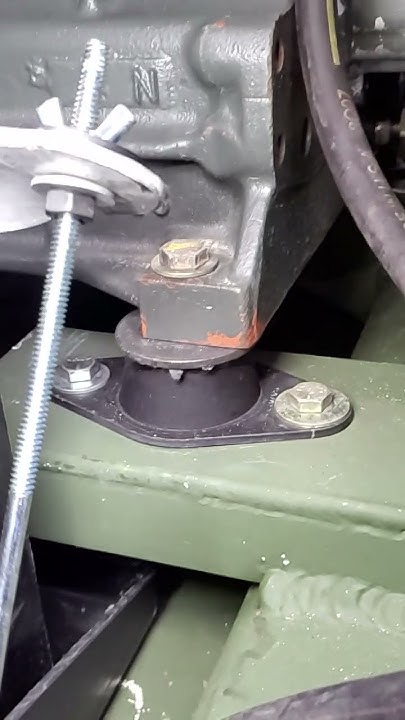
MEP-802a Paint Shaker, slow motion right front isolator
Slow motion video of the right front engine isolator of a MEP-802a generator experiencing excessive vibration. 1/30th actual speed
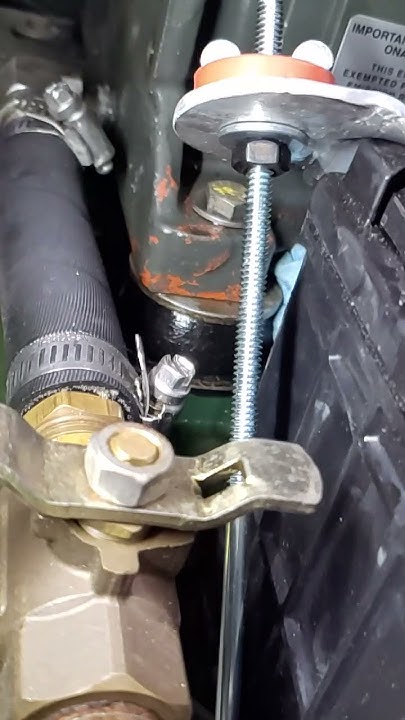
MEP-802a Paint Shaker, slow motion left front isolator
Slow motion video of the left front engine isolator of a MEP-802a generator experiencing excessive vibration.1/30th actual speed.
What do you all think?