- 280
- 506
- 93
- Location
- Indianapolis, Indiana
I've seen a few pictures showing where folks have shortened cargo beds, but I thought I would share how I did it. There are many ways to achieve this - this is just how I made a 14 foot cargo bed from an M923A2 fit on my deuce.
As you can see, the bed overhang was quite large, and it just didn't look right. It also made the pintle hitch useless.
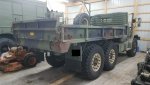
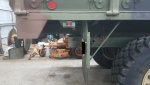
After taking off the lights and mud flaps, I cut off the entire bed rear section, 12 1/4" from the rear face. I had to cut the support rails off too, but I cut them closer to the rear, since I would be cutting them off at the proper location later.
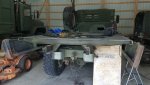
Next, I cut the slice out that I was sectioning away. In this case, it was 19 1/4". I also cut it away from the support rail structure. The cheapo plasma cutter was great for this.
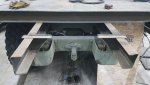
Next, I cut the remaining stubs of the support rails away from the rear section.
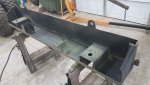
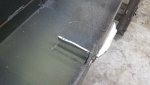
By measuring off the pieces I just cut off the rear section, I then knew how long the support rails had to be, and the size of the cut out at the bottom of them. I measured and cut the support rails to match that. So by doing it this way, I avoided having to weld the entire support rail structure. I just had to do the welds on the brackets at the rear - much easier in my opinion than cutting the whole structure in the same place.
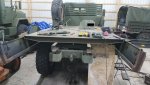
Then I tacked the rear section back in place.
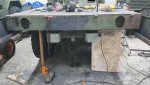
Then I moved on to the drop sides. I sectioned them at the rear of the next to last bow support location, along the existing weld. I figured that would hide more of the seam than if I just cut it out of the middle of the flat panel.
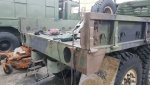
At that point, the 'hard work' was done. I just had to weld it all up, grind down a few welds where I thought it would look better smoothed out, and then re-mount the mud flaps and lights. I chose to drill through the mud flap brackets and bolt them through the bed rather than welding them on. If I was shoveling gravel out of the bed every day I would re-weld them on, and I may still do that one day, just not now. It's fine for me like it is now.
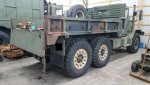
I know I work slower than a lot of people, but I probably had 25 hours of time from start to finish in this project. It wasn't all that hard to do, but it did require some patience. And it could have been done with just an angle grinder with cut off wheels, a sawzall, and the welder. The plasma cutter made a few parts of it faster, but I wouldn't consider it mandatory.
If this is something you've been putting off for several years like I did, don't be intimidated to do it. It's not as bad as you might think!
As you can see, the bed overhang was quite large, and it just didn't look right. It also made the pintle hitch useless.
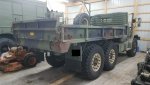
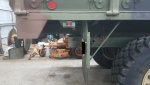
After taking off the lights and mud flaps, I cut off the entire bed rear section, 12 1/4" from the rear face. I had to cut the support rails off too, but I cut them closer to the rear, since I would be cutting them off at the proper location later.
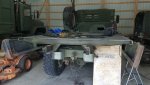
Next, I cut the slice out that I was sectioning away. In this case, it was 19 1/4". I also cut it away from the support rail structure. The cheapo plasma cutter was great for this.
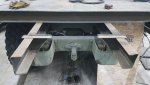
Next, I cut the remaining stubs of the support rails away from the rear section.
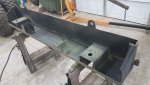
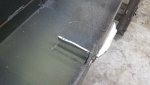
By measuring off the pieces I just cut off the rear section, I then knew how long the support rails had to be, and the size of the cut out at the bottom of them. I measured and cut the support rails to match that. So by doing it this way, I avoided having to weld the entire support rail structure. I just had to do the welds on the brackets at the rear - much easier in my opinion than cutting the whole structure in the same place.
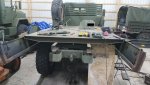
Then I tacked the rear section back in place.
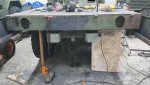
Then I moved on to the drop sides. I sectioned them at the rear of the next to last bow support location, along the existing weld. I figured that would hide more of the seam than if I just cut it out of the middle of the flat panel.
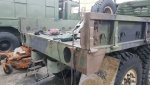
At that point, the 'hard work' was done. I just had to weld it all up, grind down a few welds where I thought it would look better smoothed out, and then re-mount the mud flaps and lights. I chose to drill through the mud flap brackets and bolt them through the bed rather than welding them on. If I was shoveling gravel out of the bed every day I would re-weld them on, and I may still do that one day, just not now. It's fine for me like it is now.
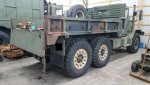
I know I work slower than a lot of people, but I probably had 25 hours of time from start to finish in this project. It wasn't all that hard to do, but it did require some patience. And it could have been done with just an angle grinder with cut off wheels, a sawzall, and the welder. The plasma cutter made a few parts of it faster, but I wouldn't consider it mandatory.
If this is something you've been putting off for several years like I did, don't be intimidated to do it. It's not as bad as you might think!