Be sure to click on the photo links, not sure why it’s doing that I have a new phone and haven’t figured it out yet.
After removing the AC compressor, winch disconnect, alternator, and turbo assembly. You finally gain access to the filter housing that has the oil cooler behind it. Pay attention to bolt lengths I had 3 different lengths of M8 bolts holding the filter housing on.
View attachment 932323
After getting the cooler out and the gasket removed, cleaned it up and yes it was not flat. Putting a straight Starrett 12” straight edge ruler left to right it was touching on both ends with a gap in the middle. I was completely ready to do whatever necessary to machine it sand it or whatever to make it flat. But before I jumped into anything I decided to investigate every aspect and consider all alternatives. The original gasket 7E9817 was carefully removed in various sections and measured. Around the perimeter it was pretty consistent at .041 - .042, in the middle where you would suspect the problem to be it measured .043 - .044. Also noted the gasket was stuck very well to the aluminum filter housing pretty much every where mainly because that side of the gasket has some sort of red adhesive strips on it. No signs of oil passing through any of the gasket areas in question. So what’s going on? The new gasket is made of a sandwiched piece of metal with thin gasket material on both sides and raised channels in the matting areas. It appears the gasket is designed to work on two different filter housings because in the wider areas have of the gasket doesn’t come in contact with the filter housing.
Back to the warp problem! If I machine one surface of the oil cooler it’s going to be flat on one side and still warped on the other side making the thickness thinner on the ends and thicker in the middle. Which can cause other problems. If you do it this way now you have a flat engine block, a flat spacer the a non flat matting surface then a flat matting surface to the filter housings. What going to happen when you tighten all the perimeter bolts something has to bend and flex. The new gasket was only .010 in the flat area and .020 in the raised channel area.
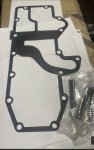
I did want to create another problem so I needed to do some more investigating. Cleaned all the matting surfaces and measured everything. The block is flat. The space is flat and same thickness throughout. The plate on the oil cooler is not flat but has the same thickness throughout measuring .2198 - .2200. Next how can I test to see how flexible the oil cooler plate is?
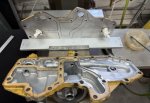
I put it in the vise on my mill with a 3” x 3/8” flat bar aluminum on each side closed the vise until it just barely came contact with the cooler plate still showing its warped I checked with feeler gages and it was .010” out. To my surprise it took very little effort tightening the vise and the cooler plate flattened out easily. Just how easy did it again with a digital torque wrench and it only took 10 flbs to get it to flatten out. So the perimeter bolts can easily manage that but what about the areas in question I outlined them out with red markings and with the vise just tight enough to make it flat and only on one side. I took a 6” straight edge and put it across those areas.
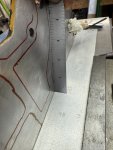
And the result is, it’s flat.
A long story short after all this I decided not to machine or modify the cooler plate and believe the original thicker gasket design could be the bigger problem and that the new gasket design is the solution. One of my biggest decision factor was if I machined the cooler plate most likely it would force the uneven surface to the cast aluminum filter housing which could potentially cause it to crack or cause other leaks in different areas.
Fingers crossed hopefully I made the right
decision.
After painting and reassembly.
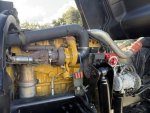