Ok, i just helped someone with this same issue, the system deflated all the tires, out in the middle of nowhere… it was a clogged vent…
like I described in the deflate cycle, control seals the PCU, then supply pressurizes it, then deflate connects the PCU to a 6.5PSI relief that drops the PCU pressure to 6.5, and the dumps copy this by dumping tire air trying to get to that same pressure.
OK, you have closed control, given a shot of supply to pressurize and open the wheel valves. Now when you turn off the ign power or pull the control jumper, the control valve should open and vent the PCU to 0, the dump valves should pass that 0 PSI along to the wheel valves that should close(causes a brief dump valve vent).
The control dumps the air from the PCU into that lower plastic cover on the bottom(Covers the solenoid coils). That cover has a fitting that is connected to a port in the floor. Now imagine what would happen if that vent out thru the floor became partly or mostly clogged and the pressure could not drop cleanly to zero. You know like when you select deflate and that 6.5 PSI relief keeps the manifold around 6-7 PSI?
The dump valves don't care what your intent was, they pass the pressure along to the wheels and if it is still enough to keep the wheel valves open, the tires will flow air back to the dump valve vents.…
check that the control vent floor passage is completely clear. Have had a few issues I assisted with where insects have closed that port with mud… it is either that or the control valve is not opening cleanly/fully.
If it is not a clogged floor vent The valve comes apart fairly easily with Oring seals. de-install the valve and remove the bottom cover, then remove the 6 Allen head screws that hold the the two halvs of the valve block together. Here is a pic of a friends valve I opened up(he had a dryer fail internally) got quite a bit of crap out of the valve and the pressure sensor was clogged with crap. There is a little spring on the bottom end of each core, make sure you don’t loose track of it, and a little dab of grease will hold it in place when you re-install the core. i believe Superman has rebuild cores and seals if you need them.
you can start the truck, close the control solenoid and pulse the supply solenoid to add air back to the tires. Low tires will drop the wet tank to the protection cutoff of 85 PSI in about 3 seconds, so 3 seconds on and 15-20 seconds off(till dryer purges). Use a tire gauge to periodically check the fill progress, don’t over-fill the tires, remember the air filled bomb part? This goes faster if you bump up the idle a bit, but it still takes quite a while
remember disconnecting port “C” from the manual page you posted earlier. If you disconnect it, that will vent the system down to the dump valves to 0 and cause the tire valves to close. This will get you back on full tires until you figure out whats up with the control not venting cleanly to atmosphere…
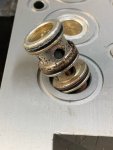