booze_rooster
New member
- 20
- 21
- 3
- Location
- Rhode Island
Hey guys, I'm here with another issue. 1952 Dodge M37 for reference.
I pulled the pinion flanges off when I removed the differentials to inspect, clean, mask, sand blast and repaint. Removed the old seals, cleaned up the machined surface and drove in new style double lip seals. I procured two Timken/SKF 99187 Speedi-Sleeves for the pinion flanges as well.
One of my two differential flanges has a large circular "shield" welded onto the shoulder. None of my parts diagrams or research show any that look like it on these trucks- but since I removed it from the vehicle, I assumed it must be a Bubba upgrade back in the day to protect the rear pinion seal face.
I pressed on my Speedi-Sleeve with green loc-tite which nicely bottoms out on the back of the shield- HOWEVER: The sleeve is much shorter than the overall length of the pinion flange's "shaft". Test fitting the flange into the seal, it seems to me that the sleeve only makes it as deep as the felt outer wiper and doesn't interface with the rubber seal further into the differential- can anyone shed light on this? I specifically have SKF 99187's.
Secondly- When I managed to get the RTV on the splines and tap the flange with the shield onto the rear diff pinion, I locked the pinion flange in place with a pipe wrench around the flange periphery braced against the garage floor and I started torquing the nut down to the specified 300 ft/lb (checked this figure in both of my manuals.) I went in stages to give my arms a break, going to 100, 200, 250, 300, then a little more to align the castle nut grooves with the hole. It was murder, but I got there.
Satisfied with my work, I went to test spin the flange before kicking the creeper back out and found the pinion was immovable. I tried putting the socket and wrench back on it figuring the new seals and sleeves would cause a little more resistance, however I couldn't budge it with a breaker bar. Before the RTV could set, I ripped the pinion nut back off with the ol' Milwaukee 1/2" impact and a definitely-not-impact rated 1 5/16" socket. Got a jaw puller on the pinion flange and zipped that back off. The pinion shaft spins normally with the flange removed.
On closer inspection, the back of the shield had a circular gouge from where it was crushed against the third member housing. (See attached photos). The shield also drove my pinion seal about 1/8" deeper into the differential housing. Clearly, the shield is causing a clearance issue and as it can't be located in this configuration in any M37 parts diagram or in any of the old Dodge flanges pictured in the VPW catalog- it must be a Bubba Build. I'm fairly certain I can buzz the four welds that hold it on, heat the speedi sleeve and press the whole thing back apart to salvage the original flange instead of shelling out $50 for a new one. However, examining my "stock one" instead of a hard shoulder at the end of the sealing surface, it just flares out. How does one go about pressing on the speedi-sleeve without a definitive shoulder to stop at? Without the shield that's welded on, the already "too short" looking sleeve will ride even further out of the differential and not cause the surface of the new sleeve to engage with the lip of the pinion seal.
In summary, my questions are- What's the deal with the Speedi-Sleeves? Do I have the wrong ones? Could I get a little technical assistance here?
On the left we have the "stock" pinion flange, on the right we have the "modified" flange.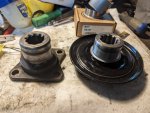
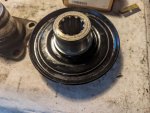
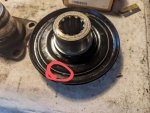
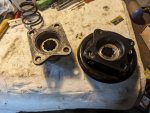
I pulled the pinion flanges off when I removed the differentials to inspect, clean, mask, sand blast and repaint. Removed the old seals, cleaned up the machined surface and drove in new style double lip seals. I procured two Timken/SKF 99187 Speedi-Sleeves for the pinion flanges as well.
One of my two differential flanges has a large circular "shield" welded onto the shoulder. None of my parts diagrams or research show any that look like it on these trucks- but since I removed it from the vehicle, I assumed it must be a Bubba upgrade back in the day to protect the rear pinion seal face.
I pressed on my Speedi-Sleeve with green loc-tite which nicely bottoms out on the back of the shield- HOWEVER: The sleeve is much shorter than the overall length of the pinion flange's "shaft". Test fitting the flange into the seal, it seems to me that the sleeve only makes it as deep as the felt outer wiper and doesn't interface with the rubber seal further into the differential- can anyone shed light on this? I specifically have SKF 99187's.
Secondly- When I managed to get the RTV on the splines and tap the flange with the shield onto the rear diff pinion, I locked the pinion flange in place with a pipe wrench around the flange periphery braced against the garage floor and I started torquing the nut down to the specified 300 ft/lb (checked this figure in both of my manuals.) I went in stages to give my arms a break, going to 100, 200, 250, 300, then a little more to align the castle nut grooves with the hole. It was murder, but I got there.
Satisfied with my work, I went to test spin the flange before kicking the creeper back out and found the pinion was immovable. I tried putting the socket and wrench back on it figuring the new seals and sleeves would cause a little more resistance, however I couldn't budge it with a breaker bar. Before the RTV could set, I ripped the pinion nut back off with the ol' Milwaukee 1/2" impact and a definitely-not-impact rated 1 5/16" socket. Got a jaw puller on the pinion flange and zipped that back off. The pinion shaft spins normally with the flange removed.
On closer inspection, the back of the shield had a circular gouge from where it was crushed against the third member housing. (See attached photos). The shield also drove my pinion seal about 1/8" deeper into the differential housing. Clearly, the shield is causing a clearance issue and as it can't be located in this configuration in any M37 parts diagram or in any of the old Dodge flanges pictured in the VPW catalog- it must be a Bubba Build. I'm fairly certain I can buzz the four welds that hold it on, heat the speedi sleeve and press the whole thing back apart to salvage the original flange instead of shelling out $50 for a new one. However, examining my "stock one" instead of a hard shoulder at the end of the sealing surface, it just flares out. How does one go about pressing on the speedi-sleeve without a definitive shoulder to stop at? Without the shield that's welded on, the already "too short" looking sleeve will ride even further out of the differential and not cause the surface of the new sleeve to engage with the lip of the pinion seal.
In summary, my questions are- What's the deal with the Speedi-Sleeves? Do I have the wrong ones? Could I get a little technical assistance here?
On the left we have the "stock" pinion flange, on the right we have the "modified" flange.
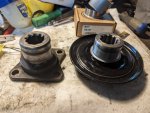
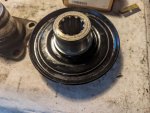
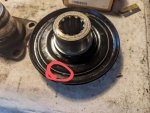
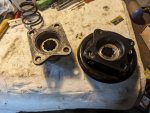