loosegravel
Just a retired mechanic who's having fun!
- 504
- 893
- 93
- Location
- Enumclaw, Washington
Well, instead of waiting to locate a different fuel pump for this unit I robbed Peter to Pay Paul. I “borrowed “ one out of my personal stand-by 10kw unit. Once the fuel system was primed it lit off. I let it run for about 10 minutes with no load. Then I began with a 25% load for about 30 minutes. Then 50% for another hour or so. I must admit. It kind of freaked me out seeing glowing embers coming out of the exhaust
When I pulled the head on this thing I didn’t remove the intake or exhaust manifolds. I can only assume (and hope!) that the exhaust manifold had a bunch of carbon in it just like the pistons looked like when I pulled them out. All of that crap was coming out when I had it under a load. At any rate, the exhaust cleared up nicely and it ran pretty good. I did have some issues getting 60hz under a load. I confirmed the gauge reading by using my Fluke. It was right on. So I grabbed my box end 8mm wrench and adjusted the bolt allowing the engine rpm to increase enough to get the hz up to 60 under a load. One thing that I’m not sure about is I’m wondering where I am as far as correct fuel pump adjustment is concerned. I reinstalled the shims that came out with each on the pumps into their perspective holes. But, because I had all of them out at the same time I should probably go through the correct adjustment process, which includes removing the gear cover and using “the special tool” they mention in the TM. Does any body have a different method that works for you. Thanks!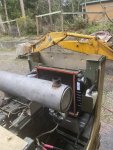
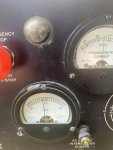
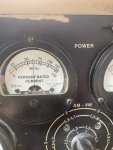
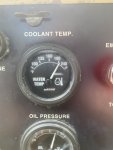
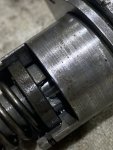
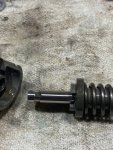
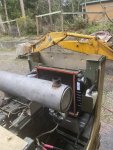
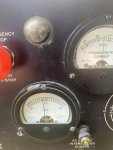
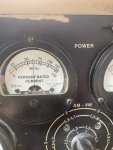
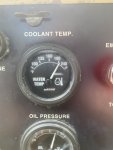
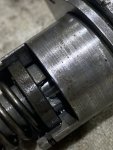
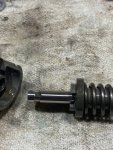