This project is very tedious. Everything is a tremendous pain in the backside. It is worth doing as I am finding corroded, worn, and vulnerable items pretty much everywhere so its good that this system is getting attention.
Not electrical, but this has bugged me for awhile. The knock out for the winch lever is just open, and I can't find a cover for this. I made one from thick rubber, using a dremel to cut a deep groove in it so it holds, the backside has adhesive so it should hold.
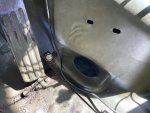
The junction box from Amazon will likely work pretty well, its fairly sturdy and fits on the (I think) regulator mount. I did need a piece of sheet metal and generally my garage has a magical property of having bits of scrap that meet whatever need I have, but it took a bit for this one. I did end up cutting up an old washer/dryer cover plate for the sheet metal, which took awhile to shape but it will work.
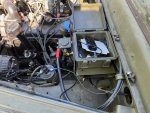
With a place to connect the various wires, I can start actually wiring stuff up. I won't reuse any of this wire, but I am leaving it until I replace it so I have some reference for what connects to what. Replacements will be in loom, I started with key ignition set and am very happy with the protective wrap plus fabric tape combo
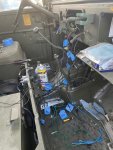
I did run into a snag, the starter solenoid post does not have enough room anymore and I am not sure what to do. The thicker battery cable is good but the alternator and two ring terminals need to go there too. One ring going to ignition via ballast and the other going to fuse box. Do they make a solenoid with a longer post?
Not electrical, but this has bugged me for awhile. The knock out for the winch lever is just open, and I can't find a cover for this. I made one from thick rubber, using a dremel to cut a deep groove in it so it holds, the backside has adhesive so it should hold.
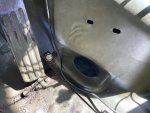
The junction box from Amazon will likely work pretty well, its fairly sturdy and fits on the (I think) regulator mount. I did need a piece of sheet metal and generally my garage has a magical property of having bits of scrap that meet whatever need I have, but it took a bit for this one. I did end up cutting up an old washer/dryer cover plate for the sheet metal, which took awhile to shape but it will work.
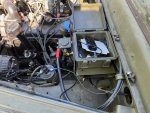
With a place to connect the various wires, I can start actually wiring stuff up. I won't reuse any of this wire, but I am leaving it until I replace it so I have some reference for what connects to what. Replacements will be in loom, I started with key ignition set and am very happy with the protective wrap plus fabric tape combo
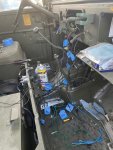
I did run into a snag, the starter solenoid post does not have enough room anymore and I am not sure what to do. The thicker battery cable is good but the alternator and two ring terminals need to go there too. One ring going to ignition via ballast and the other going to fuse box. Do they make a solenoid with a longer post?
Last edited: