- 2,482
- 6,030
- 113
- Location
- Portland, OR
I've been fighting my air system not holding (perfect) pressure overnight since I bought this truck in '21. Even after fixing every leak I could find, the pressure would drop overnight - depending on ambient temperature - usually from full tanks to about 60 psi but at times if it was fairly cold down to 30 psi or so. Colder temps would make it leak worse. I fixed literally dozens of factory push connect air line fittings - they used plastic push connect fittings all over under the dash, etc. I completely rebuilt the PUREst dryer with every kit HALDEX has available for it including a new heating element, etc - It got better but still varied according to temp and I just could not find any leaks.
Then one day a few months ago I heard something at the dryer but no amount of soapy water would show anything - after feeling around I got the leak to change tone a bit when my hand was over the main pressure relief valve on the bottom of the unit. This guy:
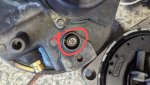
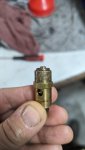
The problem is it's down in a hole (soapy water can't get down to the leak since this port is upside down on the truck) and at first I though it was the valve itself - a part that HALDEX doesn't sell
. Turns out it wasn't - the leak was from around the (new) o-ring that seals this valve to the housing. What I found is that the o-ring sealing surface down inside the hole is damaged or defective and even after replacing the o-ring and trying a couple different sizes and Molykote 111 it just would not seal up. Cursory inspection it all looks fine (it's a fairly deep pocket, it's small, and it's upside down):
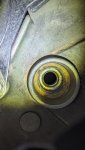
But on CLOSE inspection the problem is revealed and the "fix" is not necessarily obvious. Could likely make a tool to recut the seat for the valve. Maybe some careful application of epoxy could allow the o-ring to seal sufficiently..... I just decided to get a new old stock surplus dryer for $450 because the reality is that it comes with a new cartridge which is about $120 anyway so $330 for a guaranteed fix was worth it to me to (potentially at that point) fix my years of frustration with my truck not holding air.
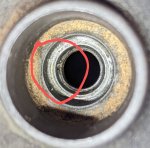
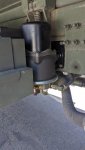
And the next morning (14 hours later) I have over 105 psi in both tanks!
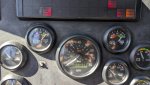
Some pressure drop is expected due to the air tanks cooling off overnight from operating temp and it's not necessarily at exactly 125 when shut down since the brakes get used to stop and apply the parking brake but it doesn't take enough to load the compressor and top itself off before shut down.
Then one day a few months ago I heard something at the dryer but no amount of soapy water would show anything - after feeling around I got the leak to change tone a bit when my hand was over the main pressure relief valve on the bottom of the unit. This guy:
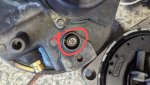
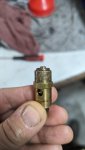
The problem is it's down in a hole (soapy water can't get down to the leak since this port is upside down on the truck) and at first I though it was the valve itself - a part that HALDEX doesn't sell

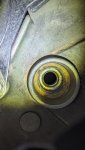
But on CLOSE inspection the problem is revealed and the "fix" is not necessarily obvious. Could likely make a tool to recut the seat for the valve. Maybe some careful application of epoxy could allow the o-ring to seal sufficiently..... I just decided to get a new old stock surplus dryer for $450 because the reality is that it comes with a new cartridge which is about $120 anyway so $330 for a guaranteed fix was worth it to me to (potentially at that point) fix my years of frustration with my truck not holding air.
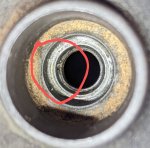
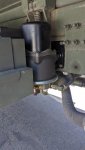
And the next morning (14 hours later) I have over 105 psi in both tanks!
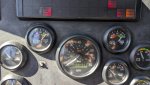
Some pressure drop is expected due to the air tanks cooling off overnight from operating temp and it's not necessarily at exactly 125 when shut down since the brakes get used to stop and apply the parking brake but it doesn't take enough to load the compressor and top itself off before shut down.
Last edited: