So after checking grounds and replacing brake/signal lamp sockets on my M1009 because of intermittent failure that turned to abject failure, I finally figured out what exactly the problems was.
The OEM socket, seen here with a metal ring flange
that the bulb lugs lock into, had become corroded. Positive connections became impossible. I replaced the sockets on rear left/right with two replacements that had NO metal ring and lug locks. The bulbs seemed to work great for awhile but after a few road trips I began to have failures in first one, and then the other. The second photo shows a black core
with plastic lug grooves instead of metal lug locks.
The third photo shows a different brand with a white core
and no metal to keep the lugs locked down so the twin bulb terminal can make constant contact with the current carrying spring bands at the bottom of the core. Both of these plastic only sockets failed.
The problem I found was that the lamp base, one copper the other bulb stainless, were climbing out of the lamp socket and losing contact with the current bands below. This was happening because as the socket became heated over long night trips; the lugs on the base heated up and melted new grooves in the plastic. The bulbs were working themselves higher and higher away from the power supply. The grounding tabs were still pressing against the bulb case, so it wasn't a grounding issue. To verify, all I had to do was press the inserted bulb down into the socket. It would light in all respects. But if I flicked the side of the socket with my finger I could see the whole bulb climb out of the socket, lose contact and go out. The whole sequence was repeatable.
My FIX: I recovered the original socket (pic 1) and dressed all points of contact with a small file. Then I spliced the original back into the wiring. The result: No climbing, only a reliable connection. While I was putting away my tools, I found a replacement socket from PICO- Part 5402C.
It had the metal ring and lug locks.
If you are having brake/signal lamp failures- which apparently make my EMERGENCY FLASHERS fail as well, try cleaning metal contacts- if you still have them. If not, be leery of the plastic core type replacement.
My Emergency Flashers did not work when the sockets failed, but worked immediately after I replaced the plastic sockets with metal OEM types.
The OEM socket, seen here with a metal ring flange
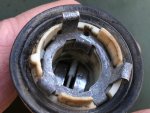
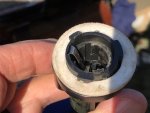
The third photo shows a different brand with a white core
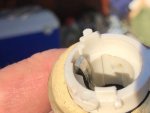
The problem I found was that the lamp base, one copper the other bulb stainless, were climbing out of the lamp socket and losing contact with the current bands below. This was happening because as the socket became heated over long night trips; the lugs on the base heated up and melted new grooves in the plastic. The bulbs were working themselves higher and higher away from the power supply. The grounding tabs were still pressing against the bulb case, so it wasn't a grounding issue. To verify, all I had to do was press the inserted bulb down into the socket. It would light in all respects. But if I flicked the side of the socket with my finger I could see the whole bulb climb out of the socket, lose contact and go out. The whole sequence was repeatable.
My FIX: I recovered the original socket (pic 1) and dressed all points of contact with a small file. Then I spliced the original back into the wiring. The result: No climbing, only a reliable connection. While I was putting away my tools, I found a replacement socket from PICO- Part 5402C.
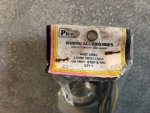
If you are having brake/signal lamp failures- which apparently make my EMERGENCY FLASHERS fail as well, try cleaning metal contacts- if you still have them. If not, be leery of the plastic core type replacement.
My Emergency Flashers did not work when the sockets failed, but worked immediately after I replaced the plastic sockets with metal OEM types.
Last edited: