I want to thank you all for the volume of knowledge on this website about these military machines. You inspire all of us that aspire to be DIY mechanics.
I have a MEP003 with a modified exhaust that allowed water to get into the engine. The exhaust pipe was installed straight up and then stored outside...
The engine is seized and I have been following some threads on water in the 803 gens engines but there is not a lot of information for the 003a since the exhaust are usually installed with a downward orientation.
I have siphoned off most of the water from the exhaust and mufflers, removed the shroud and trying to remove the fuel injector nozzles to inspect the chambers, siphon any sitting water and put some of the suggested mixtures into the cylinders in an attempt to free them.
Thank you.
Gaprime
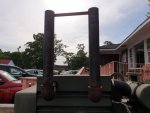
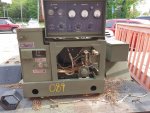
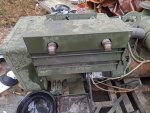
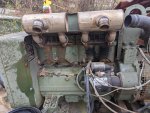
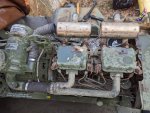
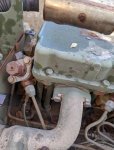
I have a MEP003 with a modified exhaust that allowed water to get into the engine. The exhaust pipe was installed straight up and then stored outside...
The engine is seized and I have been following some threads on water in the 803 gens engines but there is not a lot of information for the 003a since the exhaust are usually installed with a downward orientation.
I have siphoned off most of the water from the exhaust and mufflers, removed the shroud and trying to remove the fuel injector nozzles to inspect the chambers, siphon any sitting water and put some of the suggested mixtures into the cylinders in an attempt to free them.
- Some of the flange nuts are rusted and difficult to remove so I've soaked them with penetrating oil and trying to get a claw foot adapter... I don't want to break any of the lines - is there an easier way to get them off?
- How do you remove the injector nozzle after you remove the fuel lines and the retaining bolts and flange?
Thank you.
Gaprime
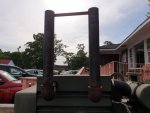
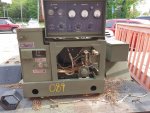
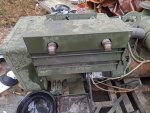
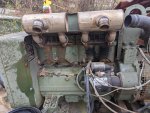
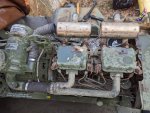
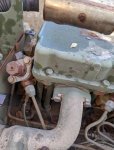