This is a continuation of the Picked up 6 MEP-802A gensets and will be documenting making them all runners here thread.
This thread is specifically about the unit where the ammeter is showing a very low reading.
I know the ammeter itself is ok since I swapped it with the one in my 803 set, where it was working fine.
I have my meter connected in series with the ammeter as follows:
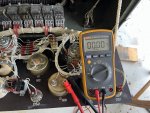
I did some additional load testing today, after straightening out all the panels and doors and putting them on the set.
I started out like this:
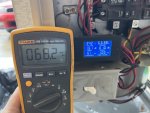
And progressed to this:
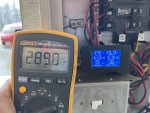
Here's a table of the loads I used:
My understanding is that the current flowing through the ammeter should be 1000 mA @ 133% load, which would be around 6,650 Watts. The closest load I was to to do, was 7,088 Watts, which only produced 255 mA as measured by my meter.
Other than the ammeter reading low, the set seems to be performing better and better as the rings are seating. Only a 2 Hz drop from a 2 kW load to a 8kW load is pretty good I think.
The overload protection would have probably kicked in after a couple of minutes of running at 8,000 Watts, but I only ran at that load for about a minute.
I didn't recheck the voltages across R10-R12 on the runs today, but I took the following readings a few days ago:
Any idea what could be causing the ammeter to read about 25% of what it should be?
On a side note, one of the reasons I didn't slap the panels on right away, is that they were all in pretty bad shape:
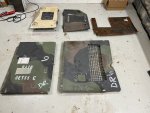
Especially the roof over the engine:
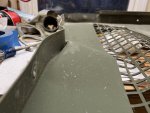
But it looks a lot better now:
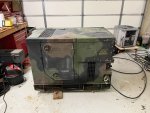
After getting the document door straight, I even painted it to get it kinda close to match the rest of the panels on that side:
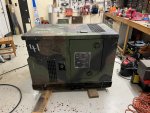
Its not perfect, but at a causal glance, I think it looks ok. Still need to work on the fuel tank cover. As you can see if the photo above of all the panels, the one on this set was made out of steel! I'll have to sand it down and prime it before putting it back on. Other than being made out of steel, it matches my other fuel tank covers perfectly, louvers and all.
This thread is specifically about the unit where the ammeter is showing a very low reading.
I know the ammeter itself is ok since I swapped it with the one in my 803 set, where it was working fine.
I have my meter connected in series with the ammeter as follows:
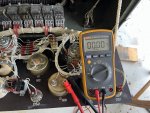
I did some additional load testing today, after straightening out all the panels and doors and putting them on the set.
I started out like this:
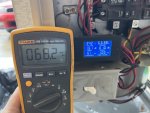
And progressed to this:
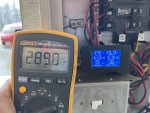
Here's a table of the loads I used:
Load 1.0 PF (Watts) | Load 0.8 PF (Watts) | Ammeter reading (mA) | Frequency (Hz) |
1,610 | 2,013 | 68.2 | 61 |
2,320 | 2,900 | 99.1 | 61 |
4,300 | 5,375 | 187.5 | 60 |
5,670 | 7,088 | 254.8 | 59 |
6,400 | 8,000 | 289.0 | 59 |
My understanding is that the current flowing through the ammeter should be 1000 mA @ 133% load, which would be around 6,650 Watts. The closest load I was to to do, was 7,088 Watts, which only produced 255 mA as measured by my meter.
Other than the ammeter reading low, the set seems to be performing better and better as the rings are seating. Only a 2 Hz drop from a 2 kW load to a 8kW load is pretty good I think.
The overload protection would have probably kicked in after a couple of minutes of running at 8,000 Watts, but I only ran at that load for about a minute.
I didn't recheck the voltages across R10-R12 on the runs today, but I took the following readings a few days ago:
Resistor | 2.26 kW | 4.10 kW |
R10 | 0.66 V | 1.36 V |
R11 | 0.49 V | 1.34 V |
R12 | 2.80 V | 4.96 V |
Any idea what could be causing the ammeter to read about 25% of what it should be?
On a side note, one of the reasons I didn't slap the panels on right away, is that they were all in pretty bad shape:
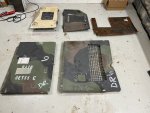
Especially the roof over the engine:
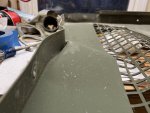
But it looks a lot better now:
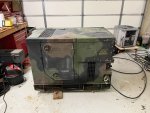
After getting the document door straight, I even painted it to get it kinda close to match the rest of the panels on that side:
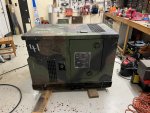
Its not perfect, but at a causal glance, I think it looks ok. Still need to work on the fuel tank cover. As you can see if the photo above of all the panels, the one on this set was made out of steel! I'll have to sand it down and prime it before putting it back on. Other than being made out of steel, it matches my other fuel tank covers perfectly, louvers and all.