- 2,306
- 4,107
- 113
- Location
- Pepperell, Massachusetts
He needs to remove the Gear End Cover over the governor. This..
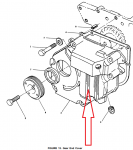
The TM calls out to insert a screwdriver through a hole in the flywheel housing to get to the ring gear (to keep the crankshaft from turning while removing bolt 5 above.)
There doesn't seem to be a hole in the flywheel housing to do this.
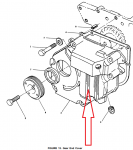
The TM calls out to insert a screwdriver through a hole in the flywheel housing to get to the ring gear (to keep the crankshaft from turning while removing bolt 5 above.)
There doesn't seem to be a hole in the flywheel housing to do this.