428gearhead
Member
- 15
- 52
- 13
- Location
- Martinsburg WV
I have been working on a 2002 MEP802A purchased from the GovPlanet auction. Original symptom was no generator output with the engine running. I dug into the exciter circuit, and found the crankshaft sensor was backed out of adjustment. After adjusting to spec, the generator "excites" and immediately bogs down the engine to the point of almost stalling. I removed all stator wires from TB3 to isolate between the generator and any downstream problems but the problem persists. I can start the engine without exciting the generator and it runs fine.
I have continuity between the correct pairs of stator leads, and no continuity between any others or any lead to ground. However, I definitely have a stator problem...
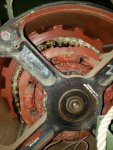
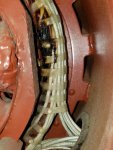
Has anyone had a stator repaired, or does anyone know where to source one at a fair price?
I'm sure there is more to this story, but this is the headliner for now.
Thanks
I have continuity between the correct pairs of stator leads, and no continuity between any others or any lead to ground. However, I definitely have a stator problem...
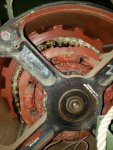
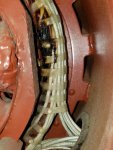
Has anyone had a stator repaired, or does anyone know where to source one at a fair price?
I'm sure there is more to this story, but this is the headliner for now.
Thanks