Got a chance to load test this set with the Stator swapped in from the spare unit. At first it was smoking a little since the new rings had not seated yet, but that cleared up after a few minutes under load. I didn't do extended load testing since I didn't have the top covers on it yet.
It does smoke a little during the 6,200 watt test, but I think that is to be expected. The good news is that the load meter works, and the frequency meter sort of does as well, although as I increase the rpms, I can't get it to register past 59.5 Hz, but maybe it will free up after more use. Still waiting on the main AC Voltmeter from Newark and the 3 small gauges from vehiclecontrols.com, but that should be it for instrumentation on this set, unless I can't get the frequency meter to move past 59.5 Hz.
After the load testing, I got the roof pieces straightened out the best I could and with some persuasion, was able to get them installed. Its the unit in the foreground.
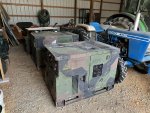
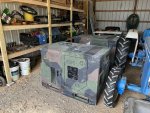
The unit behind it is the 32 hour one with a blown head gasket and the one behind it with the white siding on top, is the spare parts one. If you look closely, there is also a unit behind the Ford tractor. That's the first one I rebuild back in 2014 with the engine painted Ford Blue. That one should be good to go except I need to replace the fuel sending unit. The last one is still up in my garage, and is the one that turns over but won't fire due to low compression. I plan to tackle that one next, but will create a new thread for it.
Anyway, back to the unit I'm wrapping up, as you can see from the first picture above, its missing the control panel cover. I did get that long section of aluminum hinge and cut off a section, drilled the holes, and got it painted:
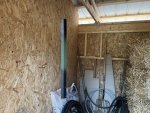
Hopefully it will bolt right up.
It does smoke a little during the 6,200 watt test, but I think that is to be expected. The good news is that the load meter works, and the frequency meter sort of does as well, although as I increase the rpms, I can't get it to register past 59.5 Hz, but maybe it will free up after more use. Still waiting on the main AC Voltmeter from Newark and the 3 small gauges from vehiclecontrols.com, but that should be it for instrumentation on this set, unless I can't get the frequency meter to move past 59.5 Hz.
After the load testing, I got the roof pieces straightened out the best I could and with some persuasion, was able to get them installed. Its the unit in the foreground.
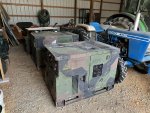
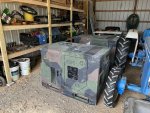
The unit behind it is the 32 hour one with a blown head gasket and the one behind it with the white siding on top, is the spare parts one. If you look closely, there is also a unit behind the Ford tractor. That's the first one I rebuild back in 2014 with the engine painted Ford Blue. That one should be good to go except I need to replace the fuel sending unit. The last one is still up in my garage, and is the one that turns over but won't fire due to low compression. I plan to tackle that one next, but will create a new thread for it.
Anyway, back to the unit I'm wrapping up, as you can see from the first picture above, its missing the control panel cover. I did get that long section of aluminum hinge and cut off a section, drilled the holes, and got it painted:
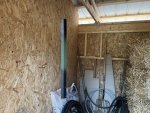
Hopefully it will bolt right up.
Last edited: