erasedhammer
Active member
- 843
- 61
- 28
- Location
- Maryland
I have a couple questions, and no these are not the normal ones that can be solved by a manual, I already have the installation instructions.
1. I have the A2 harnesses in and there appears to be a third male connector right by the horn wires.
No place for it to plug in, maybe the A2s had this connector for the 24v for the winch? (If so I assume this replaces the spliced power coming off the temp sensor)
2. I know of the trick to get the a frame bolts flipped around but I am having trouble. I jack the arm up (right under the spring) and test if the bolt is loose. Got probably an extra 8 inches up and the bolt still wasn't loose.
The nut is still on it, should I take that off prior to jacking it up? Or does it matter, cause I have a 2 ft breaker bar on it and the but isn't budging.
3. Also, is the winch bracket made of hardened steel? The holes are off on mine and I need to redrill them, wondering if I should go get some carbide drill bits.
Extra harness connector:
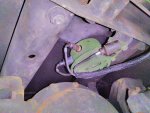
1. I have the A2 harnesses in and there appears to be a third male connector right by the horn wires.
No place for it to plug in, maybe the A2s had this connector for the 24v for the winch? (If so I assume this replaces the spliced power coming off the temp sensor)
2. I know of the trick to get the a frame bolts flipped around but I am having trouble. I jack the arm up (right under the spring) and test if the bolt is loose. Got probably an extra 8 inches up and the bolt still wasn't loose.
The nut is still on it, should I take that off prior to jacking it up? Or does it matter, cause I have a 2 ft breaker bar on it and the but isn't budging.
3. Also, is the winch bracket made of hardened steel? The holes are off on mine and I need to redrill them, wondering if I should go get some carbide drill bits.
Extra harness connector:
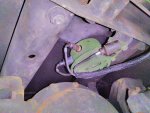