- 1,671
- 894
- 113
- Location
- Central NY
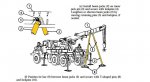
I am sure this is a common issue with a lot of wreckers - M62, M543, M246, M816, M819, M936 etc.
They lay on their sides for years without being used - the lower one can often be semi submerged depending on the angle of the bed, debris daming rain water.. The close tolerance of the two tubes promoting capillary action of water and the unpainted inside of the inner tube is prime for surface rust to build up.
I have had my boom jacks stored inside for a few years, one had been painted to the point that you cannot introduce penetrating oil into the joint. The other has been occasionally 'oiled' at the pin holes and end of the outer tube.
I have tried using the big winch on my M916A1 and a 2:1 snatch block with the boom jack shackled to the far end of a lowboy trailer - but no go.
I considered flexing the tubes - which may break the rust adhesion, but am concerned that any distortion will add to the resistance. Equally, I was not going to hammer on the outer tube for the same reason.
I had spoken to member "5ton", a retired Hotel 8 instructor, who tried using two D9 dozers to pull them apart...... to no avail.
So... I have decided to make a hyd jack press jig - to try and push the two tubes apart..
split collet
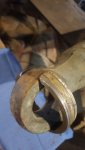
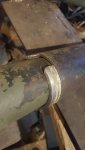
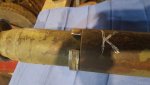
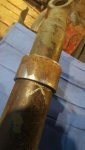
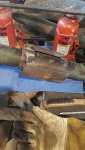
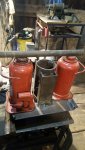
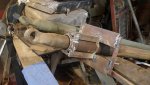
Using various scraps, I sized some collars and a split collet to go over the eye - it's a bigger diameter than the inner tube - humpf >

The channel from the collar allows room for the jacks which sit a on heavy angle base. I have two 20 ton (M916A1 Bii) jacks, and if needed, two 30 ton (M816 Bii) jacks...
Trying to visualise failure points, I beefed up weak points - hopefully. I can always add more scraps...
Next step is fabrication of the inner tube eye anchor - this needs to be close to the eye so that I do not just bend the pin that will go through it.....
(I am aware that I could tear the eye apart - however since the boom jack only works in compression, the eye isn't really a structural member and I can rebuild - in any event - the boom jacks aren't really any good to me unless they telescope! - Worst case scenario, I'll cut off the 4 ends and re-man new legs. Sourcing telescoping tube may be an issue. Could just split the outer tub length wise and cut it off with a torch and remake the outer.....)
If this works - I'd be prepared to make it available (w/o jacks) for other wrecker owners in the same situation. Possible a deposit to ensure safe return or transport to next member......
Last edited: