Toolslinger
Well-known member
- 128
- 296
- 63
- Location
- PA
Ok... Well this came to light here:
No Start - Oil Pressure - 802a
I thought I'd start a fresh thread with a more useful title to keep the further info in.
I haven't gone any further yet really. I expect it may be a slow evolution.
I found someone with a 803a enclosure that had the engine, and generator removed, due to water intrusion/locked up condition. I will probably take a look at that this week. I could see the control box wiring in the photos, and that looked fine, and it might represent some spares of other components as well. I know there's a bit of difference between 802a and 803a, but I believe the harness that I'm looking at would work, even if I had to make the odd change.
I also got an offer from someone here for some of this.
So, I expect I'll be able to come up with parts. I haven't posted a wanted yet, because quite honestly, I don't know fully what I need. I did look in the -24P, but unless I missed it, there's no PN for these harnesses complete. It seems to just tell you what the end connections are, and you build it from the specified wire gauge.
Haven't gotten the machine indoors yet. My tractor that can run a fork is tied up with a firewood trailer currently. I can sling it from a loader, but I haven't really cleared a space in the barn to set it yet. Between social schedule, work, and weather it just hasn't worked out yet. Today, I've got howling wind (~30 mph gusts), which is when we tend to loose power, but I sure don't want to be under the trees messing with it today. I got the old gas fired unit in place in case, but that's the extent of my outdoor time today. Since all the ash trees are dead/dying, any day like today is when you just hear trees crashing down in the woods. Not good outdoor weather unless you're in the middle of a field. No ash over the house, but still not ideal to be out there.
I did pull P7 apart. Unfortunately it does have enough damage that I'll have to deal with that as well. A couple pins from J7 came out when I pulled it.
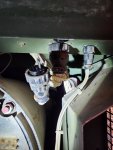
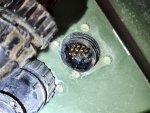
No Start - Oil Pressure - 802a
I thought I'd start a fresh thread with a more useful title to keep the further info in.
I haven't gone any further yet really. I expect it may be a slow evolution.
I found someone with a 803a enclosure that had the engine, and generator removed, due to water intrusion/locked up condition. I will probably take a look at that this week. I could see the control box wiring in the photos, and that looked fine, and it might represent some spares of other components as well. I know there's a bit of difference between 802a and 803a, but I believe the harness that I'm looking at would work, even if I had to make the odd change.
I also got an offer from someone here for some of this.
So, I expect I'll be able to come up with parts. I haven't posted a wanted yet, because quite honestly, I don't know fully what I need. I did look in the -24P, but unless I missed it, there's no PN for these harnesses complete. It seems to just tell you what the end connections are, and you build it from the specified wire gauge.
Haven't gotten the machine indoors yet. My tractor that can run a fork is tied up with a firewood trailer currently. I can sling it from a loader, but I haven't really cleared a space in the barn to set it yet. Between social schedule, work, and weather it just hasn't worked out yet. Today, I've got howling wind (~30 mph gusts), which is when we tend to loose power, but I sure don't want to be under the trees messing with it today. I got the old gas fired unit in place in case, but that's the extent of my outdoor time today. Since all the ash trees are dead/dying, any day like today is when you just hear trees crashing down in the woods. Not good outdoor weather unless you're in the middle of a field. No ash over the house, but still not ideal to be out there.
I did pull P7 apart. Unfortunately it does have enough damage that I'll have to deal with that as well. A couple pins from J7 came out when I pulled it.
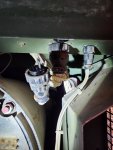
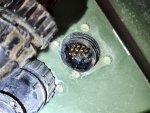