Making more slow progress. Fuel tank is replaced without a lot of drama. Well except for a neighbor that posted the below. And the neighborhood Gestapo that sited me for working on my truck MY driveway.
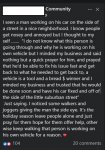
With no transmission sitting in there, I was able to remove to the two bolts for the exhaust flange on the drinker's side. I could get a wrench from the bottom along each side of the frame rail, feeling with my finger to get in seated, and the impact whirled them off.
But I am not confident I will be able to get the back of the new bolts to tighten them when I install the cross pipe with the tranny in place. Any mechanics tricks I can use and hold in place the new bolt on so I can tighten them later? I am thinking maybe put a dab of JB weld under the bolt now so maybe I can tighten the two nuts later? Any better ideas?
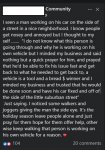
With no transmission sitting in there, I was able to remove to the two bolts for the exhaust flange on the drinker's side. I could get a wrench from the bottom along each side of the frame rail, feeling with my finger to get in seated, and the impact whirled them off.
But I am not confident I will be able to get the back of the new bolts to tighten them when I install the cross pipe with the tranny in place. Any mechanics tricks I can use and hold in place the new bolt on so I can tighten them later? I am thinking maybe put a dab of JB weld under the bolt now so maybe I can tighten the two nuts later? Any better ideas?