I bought the gauge kit from Jim after my frequency transducer went out. They look pretty good too! I love the extra information it gives me about load balancing. It was a good excuse to also put in the new panel I've had sitting on the shelf for a few months. I also did a few upgrades that I noticed in Jim's pictures, I put a waterproof switch boot on as well as 1/4 turn DZUS fasteners on the panel. I still plan on putting some SS fasteners on the DC breaker and painting it as well to match the rest of the panel.
Switch boot (quantity is 15): http://www.amazon.com/gp/product/B008DS0NWQ/ref=oh_details_o00_s00_i00?ie=UTF8&psc=1
1/4 DZUS Fastener: http://www.kurveygirl.com/shop/product_info.php?products_id=190
I could have gone up one size in diameter on the DZUS fasteners without a problem. I also could have gone 1-2mm more in length so I wouldn't have had to squeeze the retaining clip a bit, but all in all it fits just fine with a little adjustment.
(pictures of my whole project if you are interested https://plus.google.com/photos/1050...ms/5922725248166718785?authkey=CLKfr9PEpILxDA)
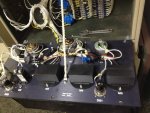
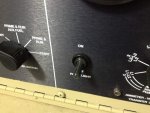
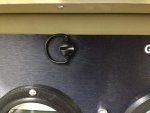
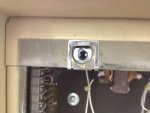
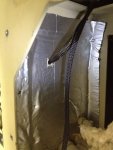
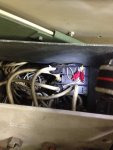
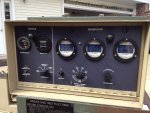
Switch boot (quantity is 15): http://www.amazon.com/gp/product/B008DS0NWQ/ref=oh_details_o00_s00_i00?ie=UTF8&psc=1
1/4 DZUS Fastener: http://www.kurveygirl.com/shop/product_info.php?products_id=190
I could have gone up one size in diameter on the DZUS fasteners without a problem. I also could have gone 1-2mm more in length so I wouldn't have had to squeeze the retaining clip a bit, but all in all it fits just fine with a little adjustment.
(pictures of my whole project if you are interested https://plus.google.com/photos/1050...ms/5922725248166718785?authkey=CLKfr9PEpILxDA)
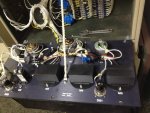
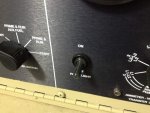
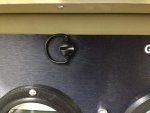
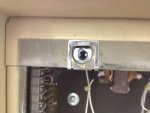
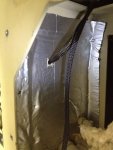
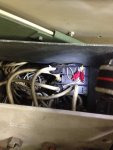
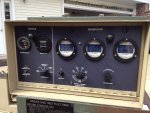
Last edited: