1oldiron
New member
- 4
- 0
- 0
- Location
- Redmond, Washington
Having purchased and installed two MEP-003A gensets, the issue of routing exhaust gases from two outlets raised some questions. Adding too much cantilevered weight of iron pipe off the muffler outlets looked to potentially create vibration and fatigue problems. Buying two long lengths of flex pipe did not seem the best idea either. Just in case anyone with a similar question might appreciate a novel approach, a photo is below along with a short description and the source of the one key part:
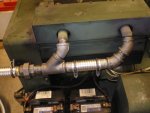
Sorry about the tiny photo. I will be glad to email a full size version if requested
Since only one 45* street elbow is required, the other had to be removed. The other issue was that the ID of the 1 3/4" flex pipe does not mate up with the OD of the 1 1/4" iron pipe. The choice was to either turn the OD of the iron pipe down to 1.380" - way too thin - and use 1 1/2" flex pipe, or build it up to fit the ID of the 1 3/4" flex pipe. Therefore the three nipples that attach to the sections of flex pipe were turned down slightly, a short piece of 1 3/4 OD exhaust tubing slipped over and brazed into place.
The key part is the 45* 1 1/4" Anvil Y. It is available from Grainger as part # 4WHU6. The rest of the stuff is off the shelf 1 1/4" elbows, nipples, and a union. If you do not have a couple huge wrenches to tighten the union, two 1 1/4 floor flanges with a chunk of Mr. Gasket header gasket material between works fine. I rigged the second unit that way since there is not a huge tool selection at the place it is installed.
You will notice the short section of flex pipe between the outlets. That is because there is no way to assemble this setup without a gap between the threaded outlets. It also compensates for the fact that a perfect alignment is basically impossible, and serves as a vibration and expansion isolator between the mufflers.
The method is to assemble the elbows and Y first and then slip the two built up nipples into the flex pipe. Then start both nipples into their respective female threads with the flex pipe in place. Once both nipples are tight, install the pipe clamps over the flex pipe.
I hope this helps a few who may still be trying to decide on the exhaust solution.
Jeff Howard
Redmond, Washington
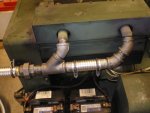
Sorry about the tiny photo. I will be glad to email a full size version if requested
Since only one 45* street elbow is required, the other had to be removed. The other issue was that the ID of the 1 3/4" flex pipe does not mate up with the OD of the 1 1/4" iron pipe. The choice was to either turn the OD of the iron pipe down to 1.380" - way too thin - and use 1 1/2" flex pipe, or build it up to fit the ID of the 1 3/4" flex pipe. Therefore the three nipples that attach to the sections of flex pipe were turned down slightly, a short piece of 1 3/4 OD exhaust tubing slipped over and brazed into place.
The key part is the 45* 1 1/4" Anvil Y. It is available from Grainger as part # 4WHU6. The rest of the stuff is off the shelf 1 1/4" elbows, nipples, and a union. If you do not have a couple huge wrenches to tighten the union, two 1 1/4 floor flanges with a chunk of Mr. Gasket header gasket material between works fine. I rigged the second unit that way since there is not a huge tool selection at the place it is installed.
You will notice the short section of flex pipe between the outlets. That is because there is no way to assemble this setup without a gap between the threaded outlets. It also compensates for the fact that a perfect alignment is basically impossible, and serves as a vibration and expansion isolator between the mufflers.
The method is to assemble the elbows and Y first and then slip the two built up nipples into the flex pipe. Then start both nipples into their respective female threads with the flex pipe in place. Once both nipples are tight, install the pipe clamps over the flex pipe.
I hope this helps a few who may still be trying to decide on the exhaust solution.
Jeff Howard
Redmond, Washington
Attachments
-
17.7 KB Views: 73
Last edited by a moderator: