Its making power!
I was getting AC voltage at the at the input to A/C interrupt, but nothing at the output. Turns out you have to push the A/C interrupt toggle switch to close momentarily begin making power...
So while it was making power, neither the voltmeter nor the load meter were working. I swapped out the voltmeter but it still didn't show anything. I decided to worry about the gauges later and moved the unit outside and connected it to my dummy load:
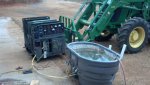
http://www.cstone.net/~dk/MEP802-11-28-2015-01.jpg
I started out with a 4500W load and my voltage was high as seen here:
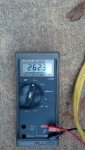
http://www.cstone.net/~dk/MEP802-11-28-2015-02.jpg
So 262 volts into a heater element rated at 4500W @ 240 volt. I had the voltage pot turned all the way down, so I guess there is a secondary adjustment somewhere?
Here's a video of running with the 4500W load:
http://www.cstone.net/~dk/MEP802power1.mp4
So the gauges that work are the coolant temp, charging and hz. After running for 3 minutes or so, the generator dropped the load and the overload indicator was lit. No sure why since my load was only 4912W (4500 / 240 * 262).
So I switched to one of the 3500W elements, and it kicked out again after a few minutes.
I guess I need to figure out why the voltage is too high and go from there. Hopefully its all related.
Another video as the unit was cooling down. Coolant temp get up there a bit! Radio in the tractor is playing Steady as she goes. Hopefully that indicative of what this generator will be doing eventually. lol
http://www.cstone.net/~dk/MEP802power2.mp4
I was getting AC voltage at the at the input to A/C interrupt, but nothing at the output. Turns out you have to push the A/C interrupt toggle switch to close momentarily begin making power...

So while it was making power, neither the voltmeter nor the load meter were working. I swapped out the voltmeter but it still didn't show anything. I decided to worry about the gauges later and moved the unit outside and connected it to my dummy load:
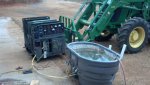
http://www.cstone.net/~dk/MEP802-11-28-2015-01.jpg
I started out with a 4500W load and my voltage was high as seen here:
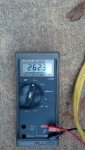
http://www.cstone.net/~dk/MEP802-11-28-2015-02.jpg
So 262 volts into a heater element rated at 4500W @ 240 volt. I had the voltage pot turned all the way down, so I guess there is a secondary adjustment somewhere?
Here's a video of running with the 4500W load:
http://www.cstone.net/~dk/MEP802power1.mp4
So the gauges that work are the coolant temp, charging and hz. After running for 3 minutes or so, the generator dropped the load and the overload indicator was lit. No sure why since my load was only 4912W (4500 / 240 * 262).
So I switched to one of the 3500W elements, and it kicked out again after a few minutes.
I guess I need to figure out why the voltage is too high and go from there. Hopefully its all related.
Another video as the unit was cooling down. Coolant temp get up there a bit! Radio in the tractor is playing Steady as she goes. Hopefully that indicative of what this generator will be doing eventually. lol
http://www.cstone.net/~dk/MEP802power2.mp4