So a couple observations after looking at this style.
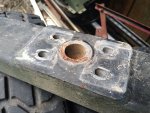
What it looks like they did (at least to me) was drill the proper size holes in the front side to fit the pintle and the bolts, then the back side they drilled oversized holes to fit spacers.
Then they added a plate over the spacer, and welded the spacers to the plate, rather than welding them into the bumper itself. The spacers are there primarily to keep the tubing from being crushed, while the plate is what handles the majority of the force being applied.
After some tack welding on the backside, they would have pulled it out and done full welds around the spacers to this added plate on the inside of it, as well as the full weld around the spacer on the outside (I only mention this because it doesn't appear to be welded to the 4 smaller spacers, only the large one in the center)
Then they welded that plate with the spacers attached to it to the back of the tubing. It wouldn't surprise me if I ground off the welds on all 4 sides of the plate in the above picture and the plate came off with all the spacers, and no welding done anywhere else.
Downside of the above style is no grease fitting, so mine didn't want to spin and took a couple whacks from a hammer to get it out.
Note: the 2" thick tubing plus the 1/4" plate welded to the back brings us to 2 1/4". The bracket on the front side where you attach the safety chains to would bring total thickness to 2 1/2". You might fit just a little more (maybe 1/8") but anything more than that and you won't be able to tighten the castle nut on the puntle down far enough to put the cotter pin through without also clamping the puntle down to immobility (it really needs to spin freely if you're driving off road with a trailer)
Edit: looking at the second picture here it also appears they machined it down or something so the plate itself where it welds is not the full 1/4" in order to be able to have a good weld that didn't need ground down afterwards, as well as allowing the castly nut to have a nice flat machined surface to spin against.