joeblack5
Active member
- 256
- 244
- 43
- Location
- State College PA
Spring has started so we got out and tried to remember what was on the agenda.
Decided to tackle some insulation, more as an experiment and to get back in the groove.
Then we drilled holes and screwed the skin with ss screws and 1/8" thick nylon washer of the bus framing to reduce with thermal bridging.. left the screws loose, added sicaflex 252 in the gap and tightened the screws.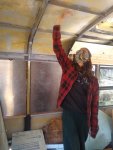
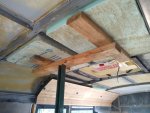
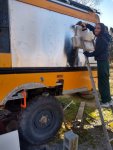
Decided to tackle some insulation, more as an experiment and to get back in the groove.
Then we drilled holes and screwed the skin with ss screws and 1/8" thick nylon washer of the bus framing to reduce with thermal bridging.. left the screws loose, added sicaflex 252 in the gap and tightened the screws.
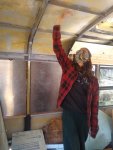
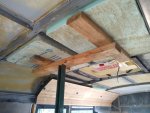
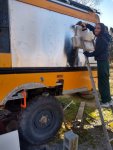