rustystud
Well-known member
- 9,396
- 3,369
- 113
- Location
- Woodinville, Washington
I have had an "on again-off again" problem with my turn signals for some time now.
The light will not go off and sometimes it will not work. Just last month I had the whole front clip off trying to find the problem. I even installed extra grounds all over the place with 10 gauge wires going straight to the battery.
So today I decided I would find this problem and fix it no matter what. I was even prepared to run whole new wires to the turn signals if I had too. So I had the right front socket out and just removed the "weatherpack" ground wire out of the socket and noticed it was totally corroded ! The inside of the socket is fine and has Dialectic grease in it to prevent corrosion, I just never pulled out the sealed ground wire !
Now I'm ordering a whole new set of turn signal sockets from LMC truck parts and will be soldering them into the wire loom.
So if anyone else has had this problem with there turn signals maybe you should also check your socket grounds. The wire pulls straight out of the socket.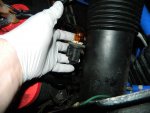
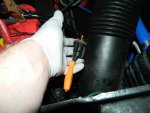
The light will not go off and sometimes it will not work. Just last month I had the whole front clip off trying to find the problem. I even installed extra grounds all over the place with 10 gauge wires going straight to the battery.
So today I decided I would find this problem and fix it no matter what. I was even prepared to run whole new wires to the turn signals if I had too. So I had the right front socket out and just removed the "weatherpack" ground wire out of the socket and noticed it was totally corroded ! The inside of the socket is fine and has Dialectic grease in it to prevent corrosion, I just never pulled out the sealed ground wire !

Now I'm ordering a whole new set of turn signal sockets from LMC truck parts and will be soldering them into the wire loom.
So if anyone else has had this problem with there turn signals maybe you should also check your socket grounds. The wire pulls straight out of the socket.
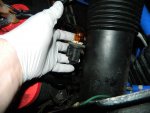
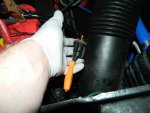