- 7,455
- 10,458
- 113
- Location
- Papalote, TX
Well hopefully this will not be the epitaph for this project, I thought a thread with the progress and possible pitfalls that lay ahead might be interesting to someone, constructive criticism, hints and comments from actual experience will be of course welcome.
Some of this has been told before but thought I would include the preface to this project.
I purchased a 2008 2500HD that had been rolled at least twice, so hard in fact all the motor mounts broke and the engine/trans/transfer went on a "walk about" but fortunately I have not seen any detectable serious damage.
When purchasing a salvage vehicle unless you are able to do a detailed inspection is is pretty much a crap shoot, SO when the donor was rolled off the wrecker and I was able to peel off enough of the body to inspect the engine I was pleasantly surprised at how nice it was and how well it test ran. It was packed with performance additions, Fleece turbo and Fleece CP-3 pump, it was set up for DSP-5 and the engine had been "built" at one time or another so even though it test ran fine the future is somewhat uncertain as with just about any used drive train, I have no intention of building a "hot rod" so the DSP-5 will say in "stock" position, the #5 position is "high idle" which might be useful for winching etc, having the complete vehicle helps insure I have all the "little" stuff like electronic gas pedal etc.
I also picked up a floor shift transfer case so I will not have to use the BCM (body control module) which is what controls the electronic version of the transfer case,
You still have to deal with 2 computers, the ECM (engine control module) and the TCM (transmission control module)
The mechanical part of the installation seems pretty straight forward, the electronic end of it is the daunting task.
There is a multitude of sensors the TCM and ECM need to do there task, THEN one normally has to add to that all the sensors the operator needs to monitor the engine (at least this seems to be the way most are doing it)
While I am not planning on "copying" anyone this crazy dude named "Johnny Magic" was showing off a conversion a friend had done and they modified the dash panel to accept the factory GM instrument cluster, this solves many problems while adding just a few, you have all the basic instruments tach, speedo (which can be "calibrated") etc, the DIC "driver information center" will be available to see any errors that pop up, but requires more work for my sheet metal guy, but this is the basic plan, the wiring harness mods cost around $500 or more and I have not found anyone willing to include the cluster wiring yet, I could add this later if I decide to get a third party to do the basic harness work. The vehicle harness will also have to be fabricated as using the factory harness is pretty much out of the question.
EDIT: turns out the LMM uses the BCM (body control module) to drive the instrument cluster unlike the earlier models so I replaced all the gauges with stepper motor type gauges and also re-wired the entire truck from headlights to tail lights and ended up using the shift on the fly TC with the TCCM.
I should have used the BCM because the LMM has the cruise control in the BCM, also manual shifting, high idle is in the BCM, I used a aftermarket fly by wire cruise control, all this is in the LBZ ECM, they had to make room in the ECM for pollution control on the LMM, next conversion will be a LBZ.
Picked up a really clean M998 with a bad motor that is an excellent donor for this project, I have 12K hubs and axles that will be installed so tomorrow the OEM engine/trans/transfer is being pulled and the project will actually begin.
Another thing that must be dealt with is the ECM/TCM programming, this MUST be done and there are two basic ways to deal with it.
1, have someone else program it, I have seen this running from $350-500 and of course if anything is missed it must be pulled and sent back or an additinal $2-300 for a downloadable programming device so the original programmer can make changes and send them to you.
2, buy your own programmer for $1200 that comes with two ECM and two TCM VIN licenses, since I already have a Duramax tow vehicle and a second M998 that may get converted at some future time this was my choice
So as you can see there is ALREADY allot to think out and do, I will post pictures as I go and name sources of the items I use.
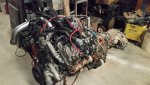
Some of this has been told before but thought I would include the preface to this project.
I purchased a 2008 2500HD that had been rolled at least twice, so hard in fact all the motor mounts broke and the engine/trans/transfer went on a "walk about" but fortunately I have not seen any detectable serious damage.
When purchasing a salvage vehicle unless you are able to do a detailed inspection is is pretty much a crap shoot, SO when the donor was rolled off the wrecker and I was able to peel off enough of the body to inspect the engine I was pleasantly surprised at how nice it was and how well it test ran. It was packed with performance additions, Fleece turbo and Fleece CP-3 pump, it was set up for DSP-5 and the engine had been "built" at one time or another so even though it test ran fine the future is somewhat uncertain as with just about any used drive train, I have no intention of building a "hot rod" so the DSP-5 will say in "stock" position, the #5 position is "high idle" which might be useful for winching etc, having the complete vehicle helps insure I have all the "little" stuff like electronic gas pedal etc.
I also picked up a floor shift transfer case so I will not have to use the BCM (body control module) which is what controls the electronic version of the transfer case,
You still have to deal with 2 computers, the ECM (engine control module) and the TCM (transmission control module)
The mechanical part of the installation seems pretty straight forward, the electronic end of it is the daunting task.
There is a multitude of sensors the TCM and ECM need to do there task, THEN one normally has to add to that all the sensors the operator needs to monitor the engine (at least this seems to be the way most are doing it)
While I am not planning on "copying" anyone this crazy dude named "Johnny Magic" was showing off a conversion a friend had done and they modified the dash panel to accept the factory GM instrument cluster, this solves many problems while adding just a few, you have all the basic instruments tach, speedo (which can be "calibrated") etc, the DIC "driver information center" will be available to see any errors that pop up, but requires more work for my sheet metal guy, but this is the basic plan, the wiring harness mods cost around $500 or more and I have not found anyone willing to include the cluster wiring yet, I could add this later if I decide to get a third party to do the basic harness work. The vehicle harness will also have to be fabricated as using the factory harness is pretty much out of the question.
EDIT: turns out the LMM uses the BCM (body control module) to drive the instrument cluster unlike the earlier models so I replaced all the gauges with stepper motor type gauges and also re-wired the entire truck from headlights to tail lights and ended up using the shift on the fly TC with the TCCM.
I should have used the BCM because the LMM has the cruise control in the BCM, also manual shifting, high idle is in the BCM, I used a aftermarket fly by wire cruise control, all this is in the LBZ ECM, they had to make room in the ECM for pollution control on the LMM, next conversion will be a LBZ.
Picked up a really clean M998 with a bad motor that is an excellent donor for this project, I have 12K hubs and axles that will be installed so tomorrow the OEM engine/trans/transfer is being pulled and the project will actually begin.
Another thing that must be dealt with is the ECM/TCM programming, this MUST be done and there are two basic ways to deal with it.
1, have someone else program it, I have seen this running from $350-500 and of course if anything is missed it must be pulled and sent back or an additinal $2-300 for a downloadable programming device so the original programmer can make changes and send them to you.
2, buy your own programmer for $1200 that comes with two ECM and two TCM VIN licenses, since I already have a Duramax tow vehicle and a second M998 that may get converted at some future time this was my choice
So as you can see there is ALREADY allot to think out and do, I will post pictures as I go and name sources of the items I use.
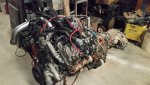
Last edited: