As mentioned earlier, I want the front and rear turn signal/stop lights to retain their original 'outward' appearance, but I want to increase their visibility when in use. One thing that I plan to do is substitute LED lamps for the original incandescent bulbs. The other thing that I want to experiment with is to repurpose the blackout marker light slot of each light to serve as an additional amber or red light. As you already know, when the original blackout light was in use, it only displayed a pair of small, dim, modified triangles.
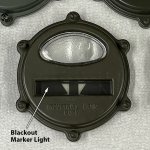
I removed the parts from the blackout marker light slot, as shown below:
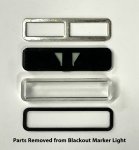
My experiment will be to replace the above parts with a section of a modern red stop light lens for the rear lights and an amber turn signal light lens for the front lights. But before doing that, I wanted to paint the light 'doors' the correct color. The two light doors shown below are for the front turn signal lights. The blackout marker light parts have been removed, and the glass lenses have been masked using a liquid "frisket" instead of masking tape, which was much easier to use than tape because of the shape of the lenses. It's important to allow the masking frisket to dry thoroughly before painting.
After spraying the light doors with Marine Corps green and allowing the paint to dry for a couple of days, it was easy to peel off the masking frisket:
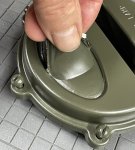
Here are the doors after removing the frisket:
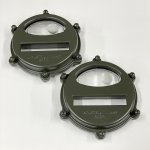
The next step will be to cut rectangular red and amber pieces out of some modern tail light and turn signal lenses for installation in the blackout marker light slots, and then try some different LED lamps to see how they compare.
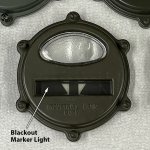
I removed the parts from the blackout marker light slot, as shown below:
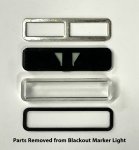
My experiment will be to replace the above parts with a section of a modern red stop light lens for the rear lights and an amber turn signal light lens for the front lights. But before doing that, I wanted to paint the light 'doors' the correct color. The two light doors shown below are for the front turn signal lights. The blackout marker light parts have been removed, and the glass lenses have been masked using a liquid "frisket" instead of masking tape, which was much easier to use than tape because of the shape of the lenses. It's important to allow the masking frisket to dry thoroughly before painting.
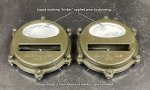
After spraying the light doors with Marine Corps green and allowing the paint to dry for a couple of days, it was easy to peel off the masking frisket:
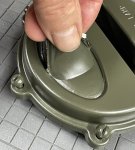
Here are the doors after removing the frisket:
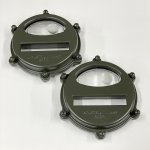
The next step will be to cut rectangular red and amber pieces out of some modern tail light and turn signal lenses for installation in the blackout marker light slots, and then try some different LED lamps to see how they compare.