rustystud
Well-known member
- 9,400
- 3,376
- 113
- Location
- Woodinville, Washington
I've been receiving a little interest in the "front servo" upgrade I posted about. I did say it is a drop in installation, but I need to clarify it a bit. You will need to cut off the pipe nut which normally threads into the servo. The later model servos did not use this nut. They just had a straight pipe go into the servo.
This is a picture of the two pipes.
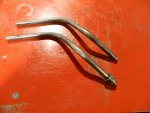
So just cut off the flare end and your Golden !
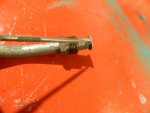
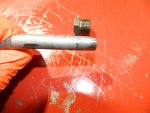
You will also need to plug this hole with a 1/8" pipe plug. Use a 21/64" drill bit and drill down 1/2" . Then tap out with a 1/8" NPT tap.
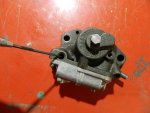
I installed a stainless steel 1/8" plug here.
Now you might get lucky if you decide to install one of these servos, but I wasn't so fortunate. It seems this servo can rub against the oil pan housing. I had to take it out several times to "remove" some material so it would fit properly.
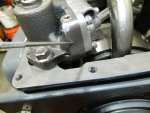
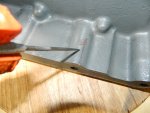
This is where it was rubbing, so removing some cast-iron on the servo until I got to the aluminum valve body did the trick.
This is a picture of the two pipes.
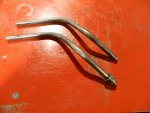
So just cut off the flare end and your Golden !
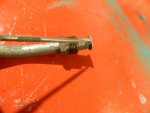
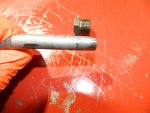
You will also need to plug this hole with a 1/8" pipe plug. Use a 21/64" drill bit and drill down 1/2" . Then tap out with a 1/8" NPT tap.
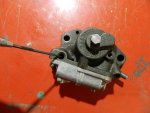
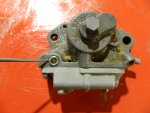
Now you might get lucky if you decide to install one of these servos, but I wasn't so fortunate. It seems this servo can rub against the oil pan housing. I had to take it out several times to "remove" some material so it would fit properly.
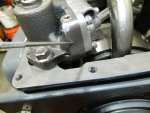
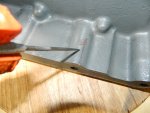
This is where it was rubbing, so removing some cast-iron on the servo until I got to the aluminum valve body did the trick.
Last edited: