Spicer 3052 3053 3053A Bearing Retainer Seal Considerations
To start with, I wasn’t planning to come out with this until the 1[SUP]st[/SUP] of the year, so I’m not quite as prepared as I’d like. It is pushing me to delve into this about a month earlier than planned. There’s suddenly a bunch of interest even though it’s been quiet for a long time. I was starting to think this was so stale that it really did not have bone-fide interest. I think what interest there may or may not be remains to be seen.
Some of you know that I suffered intermediate axle differential failure recently and it took a lot effort to complete (and the week prior to a weeklong business trip to Asia with the fridge dying the same week). And it wouldn’t have gotten sorted out at all if not for some generous help from friends (Thank You Ed for many hours of labor and Stephanie for having an axle from a bobber!). There’s always a distraction…
Similar to gringeltaube, I made a solid model of the existing part as a starting point. Looking at the wall thickness and the constraints on positioning the seal, it looked like there wasn’t a way to get a seal in there (especially assuming a big thick seal such as the front crank seal on the small block Chevy as it is very common, note this was one of my early choices). If you look at the cross-section from gringeltaube’s model it’s obvious it will not work with the big seal assumption (Benny Hill definition).
And I thought that was the end of it and I considered welding in an insert, doing a two-piece design with a weld joint, an interference fit design, etc. Then I got creative on a different path and started looking at different sized seals, ordering them, ordering more, re-modeling different scenarios, weighing the constraints, etc. Much as you would expect, I found some suppliers re-part numbering other manufacturers seals or substituting similar ones. After sorting through all that, I found three seals that are readily available (again, that is a must). And between $5-10 bucks each or so. Two of the seals would work fine and one of them I would prefer not use, although it might be OK, I just don’t have experience with that particular seal design (even though I know from cross-references that it is used in other auto applications successfully). I called one of the two BEST and would prefer to use it, again, the second choice seal should also work. I can order the most preferred seal and get several in 2-7 days. So, the availability issue is sorted out. If the thing leaks because it’s brittle 25 years from now, anyone should be able to get a replacement with reasonable effort. If any of us are around then to have that “problem” I’d consider them lucky! I don’t consider it wish to keep a spare as it is best to install a more recently manufactured seal.
I made careful measurements on the input shaft to find an acceptable engagement ring for the inner lip seal. The limitations on this position factored into the final seal bore dimensions.
So then it comes down to how much the tube portion of the bearing retainer would be compromised from a strength perspective and if there would be any distortion (say due to welding in an insert or hard and fast machining). This gets into using best practices, good decision making, engineering judgment, etc. I’m not very experienced with combating heat distortion from welding, so I’d only do that as a last resort or consult someone who knows it well. So, rule out welding if possible.
In operation the tube portion of the bearing retainer really just serves as a guide for the throw-out bearing. As such, it shouldn’t have a great deal of force acting on it as it doesn’t transfer power, bear a thrust load, used to mount the transmission, etc. It can have a bending moment or off-axis force from the throw-out bearing, most likely due to a bad pressure plate that is forcing the throw-out bearing into a cocked position. This can happen with both spring-type and a diaphragm-type pressure plates and I’ve replaced a few for that exact issue. That being said, if the pressure plate is bad and causing the throw-out bearing to be cocked around the pressure plate needs to be replaced anyway and will cause the clutch to stick. You cannot blame a bad pressure plate on the bearing retainer. Back to the main point, I analyzed the model (using Finite Element Analysis, FEA) by approximating the engagement area of the throw-out bearing and applied loads, re-ran the FEA on models with different sized seals and seal depths. I used typical assumptions in the FEA such as mild steel, constant material properties, etc. Given the shape and complexity I did not do a textbook style pen and paper analysis. After all, I pay about $1400 to maintain my CAD software, so I should get some use out of it.
The forces that might act on the tube portion of the bearing retainer while not in operation also need to be considered. The engineering analysis for both in and out of operation is similar anyway. So take for example that someone grabs the tube portion of the bearing retainer and the exit flange and lifts the transmission. Bear in mind that I don’t recommend this wouldn’t do this with this heavy of a transmission and it should be lifted by the body as the bearing retainer is not a handle, although it is standard practice for smaller transmissions. Disclaimers aside, you would not want the bearing retainer to bend if you did happen to carry it this way. The results of my FEA made it clear that you could lift this beast by the snout, that it would not plastically deform (permanent) if you did, and that machining the seal pocket did not cause a significant change in strength of the part. And then for the disclaimer, I don’t recommend anyone do anything stupid like drop the transmission out of the back of the truck onto concrete and expect there to be no damage.
Here is a snip of the cross-section of my model with the seal pocket. As you can see, it doesn’t get much thinner than the rest of the part. At first glance, (especially if you look at the big seal assumptions) it would seem that the part is badly compromised by the seal pocket. Careful analysis using modern tools and methods combined with the results of the seal search demonstrate that the addition of the seal is very plausible.
I will post more pics and hopefully a video on YouTube in the next week or so. Also, I plan to have 10 of these available later this week.
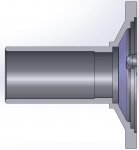